What is Decanter centrifuge?
- An industrial tool called a decanter centrifuge uses centrifugal force applied continuously to separate combinations of liquids and solids.
- It works using a quickly revolving bowl angled horizontally to generate strong centrifugal forces, therefore accelerating the sedimentation of denser particles.
- One important part is the internal screw conveyor, which rotates the separated particles around the bowl constantly so enabling continuous separation from clear liquid outputs separately.
- Leveraging the differential in density between solid particles and the surrounding liquid, the machine separates solids outward to the bowl wall where they gather.
- To effectively dewater sludges and clear liquids, decanter centrifuges find application in the food and beverage sector, chemical processing, wastewater treatment, and other areas.
- Maximizing the separation efficiency and guaranteeing energy-effective performance depend critically on operational factors like bowl speed, screw speed, and feed rate.
- For constant industrial separation problems, the design lets one handle high throughput and changeable feed conditions, therefore offering a flexible solution.
- Its strong building and changeable running parameters allow exact control over the separation process, thereby promoting better product recovery and lower waste generation.
Working Principle of Decanter Centrifuges
Operating on the basis of buoyancy, a decanter centrifuge separates While a less dense component would float on top, a component with more density would naturally sink to the bottom of a mixture. In a decanter centrifuge, constant spinning improves the speed of settling and generates a g-force between 1000 and 4000 G’s. Using a decanter centrifuge allows mixes that once needed hours to settle in a matter of seconds, therefore substantially reducing the settling duration of the components. Faster and more controllable results arise from this kind of separation.
All a decanter is is a sedimentation tank around an axis. By gravity, heavier solid particles than liquid migrate to the bottom of the sedimentation tank and create a sediment (solid phase) there. One may consider a wine decanter as a saggeter vessel. Centrugal acceleration divides the solid and liquid phases of a centrifuge. Because of centrifugal force, the solid particles—which have a higher density and consequently weight more than the liquid— move outward in the spinning bowl of the centrifuge. The inner wall of the centrifuge bowl creates the sediment on its inside. In a centrifuge, the separation of solid particles from liquid is more quick and effective as centrifugal forces of about 3000 g are used instead of 1 g in a gravitational field.
Decanter-based separation of three phases
One may separate three phases in one operation using a 3 phase decanter centrifuge. For example, a solids phase separates oil and water from each other as their densities prevent their mixing. Water accumulates in the center between the layers of solids and oil. After separation, the two liquids can therefore be extracted from the decanter. The solids are transferred from the scroll to the discharge holes via 2-phase separation, same as in other systems.
Among the common uses of three-phase separation are the production of biodiesel, olive oil, and olive oil, processing of oil sludge, and so on.
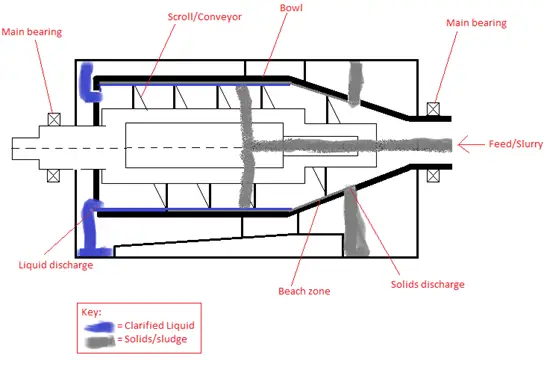
Parts of Decanter Centrifuges
A decanter centrifuge consists in many important components that cooperate to extract solids from liquids. These pieces comprise:
- The bowl – The centerpiece of the centrifuge is the bowl. Spinning on a horizontal axis, this cylindrical container looks A feed pipe feeds the mixture to be separated into a bowl; the divided solids and liquids are released from several exits.
- The scroll – Mounted within the bowl is a helical screw that forms the scroll. Driven by a motor, it spins a somewhat slower than the bowl. The scroll shows the solids headed toward the bowl’s outer wall, where centrifugal force separates them from the liquids.
- The solids discharge port – The separated solids are dumped from an exit on the bowl’s outside wall called the solids discharge port.
- The liquids discharge port – The separated liquids are dumped out an exit on the bottom of the bowl called the discharge port.
- The drive system – This covers the engine and other parts running the bowl and scroll.
- The control system- This covers the sensors and other parts meant to track and regulate the centrifuge’s running performance.
- The frame and support structure – Including the frame and other structural elements supporting the bowl and other centrifuge components, this comprises the support system.
- The feed pipe – The feed pipe is a conduit used to feed the mixture into the centrifuge bowl.
- The feed pump – Constant rate feeding of the mixture into the feed pipe is accomplished with the feed pump.
- The feed control system – Comprising sensors and other parts used to monitor and regulate the mixture’s flow into the centrifuge, the feed control system
How the Decanter Process Works
- Before start-up, check the decanter centrifuge to be sure all safety guards, bearings, seals, and discharge ports are intact and free of damage.
- Check that the centrifuge is correctly balanced and that regular maintenance has been finished to guarantee seamless running.
- Based on the particular process requirements, set the operating parameters—including feed rate, bowl speed, and differential (scroll) speed.
- Using the variable frequency drive (VFD), progressively raise the bowl’s spinning speed until the target operating speed is attained.
- Through the specified feed tube, feed slurry should be introduced into the centrifuge under constant and regulated flow.
- Let the centrifugal force separate the denser solids—forced against the inner wall—from the lighter liquid collecting at the center as the bowl turns.
- Track the separation process by noting the dryness of the released solids and the purity of the centrate; then, modify the differential speed to maximize residence time.
- Make any required real-time feed rate or rotational speed changes to preserve effective separation and stop process disruption.
- Once the run is stopped or the separation process is finished, progressively slow down the bowl speed and stop the feed system thereby enabling the centrifuge to decline gently.
- Perform a post-run inspection and cleaning to eliminate leftover materials and get the equipment ready for the next operation after the centrifuge has stopped entirely.
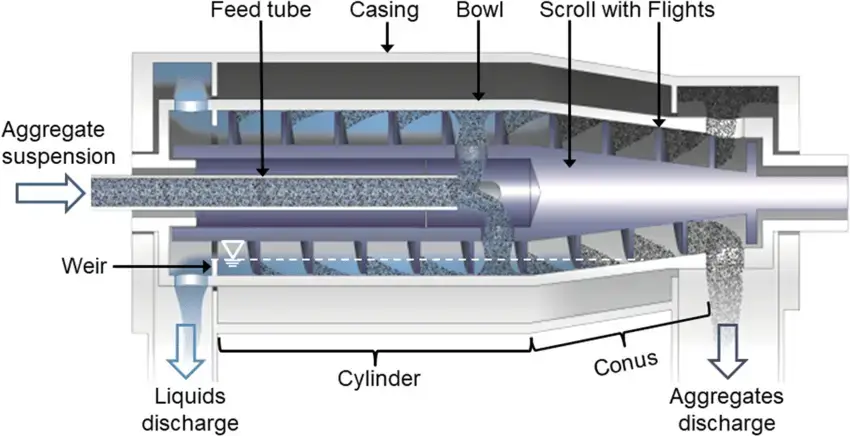
Parameters and influencing factors of the separation
- Feed, throughput, and dwell times – Feeding the to-be-processed separating medium into the center of the infeed chamber of the scroll accelerates it. The throughput will effect residence time.
- Acceleration – The separating medium in the decanter bowl achieves its highest speed, which drives solids to settle on the inner circle of the bowl. The form of the bowl is cylindrical or conical.
- Differential velocity – On industrial decanter centrifuges, a gear system produces a speed difference between the decanter bowl and the scroll. Differential speed controls the solids in the outfeed.
- Volumetric filling / Weir discs or overflow weir – The filtered liquid in a decanter centrifuge runs to the cylindrical end of the bowl where it leaves via holes in the bowl cover. These holes include precisely changeable weir discs or plates that let the bowl’s pond depth be varied. The bowl’s filling capacity is found on the weir discs.
Applications of Decanter Centrifuges
- Extensive application of decanter centrifuges in wastewater treatment plants helps to dewater biosolids and lower sludge volume, thereby improving the effectiveness of waste disposal and treatment techniques.
- They work in the food and drink sector to efficiently remove suspended particles and guarantee product purity, so clarifying liquids like fruit juices, dairy products, and edible oils.
- These centrifuges separate reaction mixtures in chemical and pharmaceutical manufacture by extracting catalysts and solid by-products from liquids, therefore simplifying downstream processing.
- Decanter centrifuges allow the oil and gas sector to extract oil from water-oil mixes and separate drilling muds, therefore reducing waste and enhancing resource recovery.
- In mining and mineral processing, they help to separate fine mineral particles from slurries, therefore enabling ore concentration and so lowering the tailings volume.
- Decanter centrifuges help the pulp and paper sector dewatering sludge, therefore minimizing transportation costs and storage needs.
- These devices are used to gather cells and clear fermentation broths in biotechnology and pharmaceutical applications, which is essential for guaranteeing high-quality downstream product recovery.
- Recycling and waste management techniques as well as specialized extraction activities such hemp processing and edible oil production—where fast and continuous separation is crucial—also find use here.
Advantages of Decanter Centrifuges
- Operating constantly, decanter centrifuges save downtime and improve process throughput by allowing continual separation of particles from liquids.
- They greatly shorten settling periods from hours to mere seconds by producing very strong centrifugal forces—up to 4000 times that of gravity, hence improving general efficiency.
- Their design enables exact change of operational parameters including bowl speed, differential (auger) speed, and pond depth, therefore enabling the process to be customized to varied feed compositions and particular industrial demands.
- Their strong structure and high throughput capacity qualify them for a broad spectrum of uses, including chemical manufacture, food and beverage processing, wastewater treatment, oil and gas activities, and mining.
- Decanter centrifuges’ dewatering capacity generates drier cake solids, which reduces storage, handling, and transportation costs and increases process economics generally.
- Their constant countercurrent architecture guarantees consistent product quality and helps high degrees of automation and process control, hence lowering labor needs.
- Accessible worn components and integrated cleaning systems help to accomplish easy of maintenance by extending equipment life and lowering long-term running costs.
Limitations of Decanter Centrifuges
- Because producing the necessary centrifugal forces requires extremely high rotating speeds, decanter centrifuges demand great energy input.
- Their advanced control systems and complicated, strong design call for large capital expenditure.
- Processing feeds with low density variations reduces their separation efficiency, thereby restricting their usefulness for very tiny or fragile particles such certain biological solids.
- High noise and vibration levels during operation might call for further dampening strategies and cautious installation to guarantee operator safety and equipment lifetime.
- Especially in abrasive applications, which can result in more downtime and running expenses, regular maintenance and worn part replacement are generally required.
- They may not function effectively with highly varied or low-volume feed streams; they are best suited for constant, high-throughput operations.
- Shear-sensitive materials might suffer from the strong mechanical stresses, thereby limiting the usage of decanter centrifuges in several delicate processing uses.
What is the difference between centrifuge and decanter?
Aspect | Centrifuge | Decanter Centrifuge |
---|---|---|
Definition | A machine that uses centrifugal force to separate components of a mixture based on density differences. | A specialized type of centrifuge designed for continuous separation of solids from liquids. |
Operation Mode | Typically operates in batch processes, requiring periodic stoppage to remove separated solids. | Operates continuously, allowing uninterrupted separation and discharge of solids. |
Design Features | May lack internal mechanisms for moving solids; separation occurs primarily through sedimentation. | Equipped with a rotating helical screw (scroll) that conveys separated solids towards discharge ports. |
Applications | Used for a variety of purposes, including density-based separation and purification of liquids. | Primarily employed in industries requiring continuous solid-liquid separation, such as wastewater treatment and food processing. |
Solids Handling | May require manual intervention to remove accumulated solids. | Automatically discharges separated solids, reducing the need for manual handling. |
FAQ
What is a decanter centrifuge used for?
A decanter centrifuge is a machine that is used to separate solids from liquids in a mixture. It is a continuous process that uses centrifugal force to separate the two components. Decanter centrifuges are used in a wide range of industries and applications, including chemical, pharmaceutical, food processing, environmental engineering, oil and gas, mining and mineral processing, power generation, and pulp and paper.
Some specific examples of what a decanter centrifuge may be used for include:
Separating chemicals, such as acids, alkalis, and solvents, in the chemical industry
Separating pharmaceutical products, such as drugs and excipients, in the pharmaceutical industry
Separating food products, such as milk and juice, in the food processing industry
Treating and dewatering sludge in wastewater treatment plants in the environmental engineering industry
Separating oil, water, and solids in drilling and production operations in the oil and gas industry
Separating minerals and other solids from water and other liquids in ore processing and beneficiation operations in the mining and mineral processing industry
Dewatering coal and other fuels in power generation operations
Dewatering pulp and paper sludge in paper mills in the pulp and paper industry
Is a decanter a centrifuge?
Yes, a decanter is a type of centrifuge. A centrifuge is a machine that uses centrifugal force to separate solids from liquids or to separate components of a mixture based on their densities. A decanter centrifuge is a specialized type of centrifuge that is specifically designed to separate solids from liquids in a continuous process.
Decanter centrifuges are characterized by their continuous operation, the presence of a scroll (a helical screw that rotates at a slightly slower speed than the bowl and conveys the solids towards the outer wall of the bowl), and a solids discharge port located on the outer wall of the bowl. They are used in a wide range of industries and applications, including chemical, pharmaceutical, food processing, environmental engineering, oil and gas, mining and mineral processing, power generation, and pulp and paper.
Why is it called a decanter?
The word “decanter” refers to a container with a wide base and a narrow neck, typically used for storing and serving wine. In the context of a decanter centrifuge, the term “decanter” refers to the shape of the bowl, which is similar to a wine decanter. The bowl of a decanter centrifuge is a cylindrical container with a wide base and a narrow neck, and it spins on a horizontal axis.
The use of the term “decanter” in relation to a centrifuge may have originated from the fact that decanter centrifuges are often used to separate liquids with different densities, such as wine and sediment. In this case, the centrifuge bowl would be similar in shape to a wine decanter and would be used to separate the clear liquid (wine) from the sediment (lees) at the bottom of the decanter.
- Text Highlighting: Select any text in the post content to highlight it
- Text Annotation: Select text and add comments with annotations
- Comment Management: Edit or delete your own comments
- Highlight Management: Remove your own highlights
How to use: Simply select any text in the post content above, and you'll see annotation options. Login here or create an account to get started.