What is Ultrasonic Homogenizers?
- Usually in the range of 20–100 kHz, ultrasonic homogenizers are devices that cause acoustic cavitation in liquids and produce strong local shear forces by means of high-frequency sound waves.
- Microbubbles provide shock waves, turbulence, and microstreaming that efficiently lower particle size and guarantee homogeneous dispersion; their development, growth, and quick collapse form the basis of action.
- Their value stems from their capacity to upset cellular structures, boost emulsification, and raise extraction efficiencies in many matrices, so improving the quality and consistency of produced goods.
- Historically, ultrasonic homogenization arose from early sonochemical research in the mid-20th century and has grown from laboratory-scale devices to industrial-scale continuous flow systems, reflecting developments in transducer design and energy control.
- Applications cover several disciplines including food processing, pharmaceuticals, biotechnology, and materials research, where low chemical use and nonthermal processes are greatly valued.
- Important design elements include ultrasonic transducers, usually coupled with horn or probe systems, which increase the displacement amplitude therefore facilitating effective energy transmission into the medium.
- Recent developments have concentrated on optimizing power input, frequency settings, and process configurations to increase repeatability and scalability while lowering energy consumption and possible heat damage.
Principle of Ultrasonic Homogenizers
- By piezoelectric transducers, which then produce ultrasonic waves in the medium, ultrasonic homogenizers transform electrical energy into high-frequency mechanical vibrations.
- Usually exceeding 20 kHz, these ultrasonic waves produce fast alternating high- and low-pressure cycles that cause acoustic cavitation in the liquid.
- By means of rectification diffusion, minute gas nuclei in the liquid expand to create microbubbles during the low-pressure phase.
- These microbubbles rapidly burst in the next high-pressure cycle to create localized hotspots with very high temperatures and pressures.
- Effective homogeneity results from the fast bubble collapse generating shock waves, microjets, and strong shear stresses upsetting big particles, aggregates, and cell structures.
- This procedure greatly lowers particle size and increases dispersion, hence improving emulsification and mixing efficiency.
- Key factors like ultrasonic frequency, power intensity, exposure length, and ultrasonic horn or probe design determine ultrasonic homogenizer performance generally.
- Important for industrial-scale uses, optimized horn designs—such as conical or barbell horns—increase the acoustic energy and guarantee effective energy transmission into the medium.
- The method maximizes homogeneity efficiency by precisely balancing energy input and processing time, therefore reducing negative thermal effects that could affect product quality.
- Where homogeneity and stability of emulsions or suspensions are crucial, these ideas support a variety of applications including food processing, pharmacological formulation, and biotechnology.
Parts of Ultrasonic Homogenizers
The specific parts of an ultrasonic homogenizer can vary depending on the type of ultrasonic homogenizer being used, but here are some common parts that are found in most ultrasonic homogenizers:
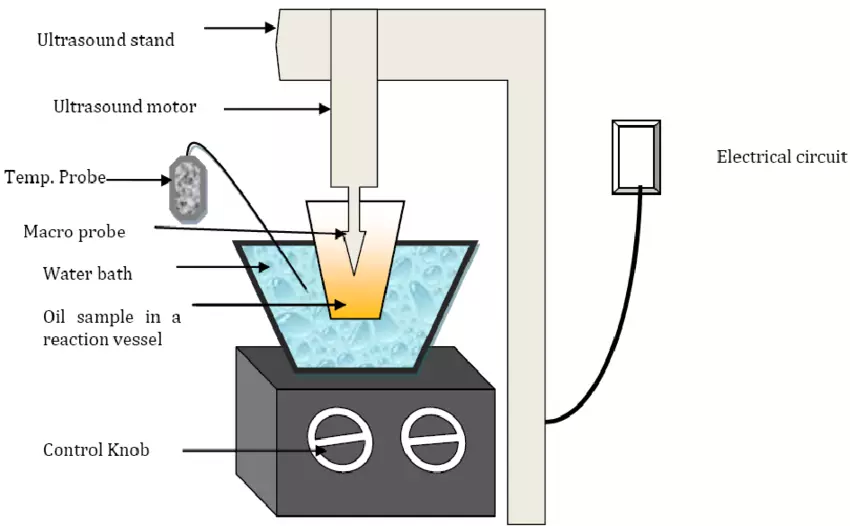
- Ultrasonic generator: This is the main control unit of the ultrasonic homogenizer. It converts electrical energy into high-frequency sound waves.
- Transducer: This is the part of the homogenizer that converts the electrical energy from the generator into mechanical energy in the form of sound waves. It is usually made of a piezoelectric material that expands and contracts when an electrical current is applied to it.
- Horn: This is the part of the homogenizer that amplifies the mechanical energy from the transducer and directs it into the liquid sample.
- Sample chamber or beaker: This is where the sample is placed for homogenization. It can be made of glass, plastic, or stainless steel.
- Power switch: This controls the power to the generator.
- Timer: This allows the user to set the homogenization time.
- Amplitude control: This controls the intensity of the ultrasonic energy and helps to ensure that the sample is homogenized to the desired particle size.
- Safety switch: This prevents the homogenizer from operating when the lid or cap is not properly secured.
- Fuse: This protects the homogenizer from damage due to power fluctuations or electrical overload.
- Additional parts may include a cooling system, pressure gauge, and sample collection vessels.
It’s important to refer to the manufacturer’s instructions for the specific ultrasonic homogenizer being used, and to follow appropriate safety precautions while working with the homogenizer.
Types of Ultrasonic Homogenizers
- Probe-Type Ultrasonic Homogenizers – Often composed of titanium, these probe-type ultrasonic homogenizers directly dip a probe into the substance. The probe generates cavitation by sending ultrasonic energy, therefore upsetting either cells or particles. Used extensively in laboratories for cell disruption and sample preparation, they are especially successful for small to medium volumes.
- Bath-Type Ultrasonic Homogenizers – Known also as ultrasonic cleaners, bath-type ultrasonic homogenizers have a sample tank. The tank walls’ ultrasonic waves cause cavitation all around the bath. Although they have less intensity than probe-type homogenizers overall, they are appropriate for processing more volume or several samples at once.
- Industrial Ultrasonic Homogenizers – Designed for mass use, industrial ultrasonic homogenizers include ultrasonic technology into manufacturing operations. Capable of continuous processing of significant volumes, they are used in food processing, pharmaceuticals, and cosmetics for jobs including emulsification, particle size reduction, and extraction.
- Laboratory Ultrasonic Homogenizers – Designed for use in laboratories, these small to medium-sized portable ultrasonic homogenizers Operating at frequencies between 20 kHz and 100 kHz, they can handle sample quantities ranging from a few milliliters to several liters, making them flexible for diverse research objectives.
- Ultrasonic Homogenizers with Barbell Horns – These homogenizers effectively broadcast ultrasonic energy into the sample using barbell-shaped horns. For high-power industrial uses including emulsification, dispersion, and sonochemical processes, the design lets ultrasonic amplitudes be amplified while keeping large output diameters.
Operating Procedure of Ultrasonic Homogenizers
- Make that the homogenizer is set on a steady, spotless surface and that all safety gear—gloves, goggles, lab coats—is available and worn.
- Before beginning the process, fully clean the probe and sample container with suitable solvents to avoid cross-contamination.
- Once the homogenizer is connected to a grounded power source, make sure all safety mechanisms and interlocks are operating as they should.
- Based on sample volume and type, choose the suitable probe; then, carefully fastened it to the device according manufacturer guidelines.
- Pre-cool the sample if necessary using an ice bath or integrated cooling system to decrease heat created during sonication.
- To enhance cavitation efficiency, submerge the probe into the sample such that it is justly buried without hitting the bottom or container walls.
- Adjust the operational parameters—amplitude, pulse mode, processing time—based on the physical characteristics of the sample and experimental constraints.
- Start the process with brief bursts to assess the impact on the sample; then, change the power and duration as necessary to attain good homogeneity.
- Track the temperature and consistency of the sample constantly while it is running and modify to stop degradation or overheating.
- Turn off the homogenizing equipment right away and gently remove the probe from the sample once homogenization is finished.
- Using suitable cleaning agents, rinse and clean the probe and sample vessel to eliminate any leftover material, therefore guaranteeing that all components are dried correctly.
- For quality control and future reference, record in the laboratory log all operational parameters, observations, and any maintenance actions.
- To guarantee long-term dependability, routinely maintain and check the probe and device; calibrate as directed by manufacturer recommendations.
Applications of Ultrasonic Homogenizers
- In microbiology and biotechnology, ultrasonic homogenizers are applied with great cavitational forces that break cell walls and membranes to extract proteins, enzymes, and nucleic acids, thereby disrupting and lysing cells.
- By efficiently mixing immiscible liquids, they form stable oil-in—water or water-in—oil emulsions, so playing a vital part in emulsification techniques in the food, cosmetic, and pharmaceutical sectors.
- These devices are applied for nanoparticle dispersion and size reduction in nanotechnology, assuring uniform particle distribution and boosting the stability of suspensions
- Accurate analytical readings and process consistency depend on the removal of entrapped air and dissolved gases from liquid samples by ultrasonic homogenizers in degassing applications.
- They help to create nano-sized vesicles that encapsulate active medicinal substances, therefore enabling the manufacture of liposomes and the evolution of drug delivery systems.
- Ultrasonic homogenization increases the release and solubilization of target molecules, so facilitating the extraction of bioactive compounds from plant or microbial sources.
- Ultrasonic homogenizers help to homogenize tissues in biochemical tests and proteomics so guaranteeing effective cell disruption and consistent sample preparation for next analysis.
- They are also used in sonochemical techniques to speed chemical reactions by enhancing mass transfer and creating localized high pressures and temperatures, so influencing reaction kinetics under controlled conditions.
Advantages of Ultrasonic Homogenizers
- By means of acoustic cavitation, ultrasonic homogenizers provide highly concentrated energy that facilitates effective cell destruction and exact particle size reduction.
- They enable exact control over processing parameters like as amplitude, pulse duration, and time, providing predictable and consistent outcomes
- Their energy efficiency usually results in homogenous emulsions and dispersions while often shortening production times.
- From laboratory to industrial uses, ultrasonic homogenizers can process a wide spectrum of sample volumes and viscosities, so enabling smooth scalability.
- Minimal moving components in their design help to lessen maintenance requirements and lower the danger of sample contamination.
- The method maintains sensitive biomolecules during cell breakdown, making it excellent for protein extraction and biochemical testing
- Their ability to create nano-sized emulsions and dispersions improves product quality in cosmetic and medicinal formulations.
- Versatile, ultrasonic homogenization supports uses including sonochemical processing, bioactive compound extraction, and degassing.
Limitations of Ultrasonic Homogenizers
- Excessive heat produced by ultrasonic homogenizers running can threaten the integrity of temperature-sensitive samples.
- Their efficiency decreases with more viscous materials since the energy from cavitation is less effectively transferred in thick fluids.
- Regular use—especially with abrasive or corrosive materials—causes probe deterioration and raises maintenance expenses.
- The high cavitation might create free radicals, potentially triggering undesired chemical changes in delicate mixtures
- Unless pre-suspended in a liquid, ultrasonic homogenization is usually inappropriate for treating dry powders or solid materials.
- From laboratory to industrial operations, scaling can be difficult since consistent energy distribution over greater volumes calls for careful optimization.
Reference
- Onaneye-Babajide, Omotola & Petrik, Leslie & Bamikole, Amigun & Farouk, Ameer. (2010). Low-Cost Feedstock Conversion to Biodiesel via Ultrasound Technology. Energies. 3. 10.3390/en3101691.
- https://www.fishersci.com/us/en/browse/90180027/ultrasonic-homogenizers?page=1
- https://www.biologics-inc.com/ultrasonic-homogenizers.html
- https://www.labcompare.com/General-Laboratory-Equipment/563-Ultrasonic-Homogenizer-Laboratory-Homogenizers-Sonicator/
- https://www.labtron.com/ultrasonic-homogenizer-sonicator
- https://www.omni-inc.com/omni-sonic-ruptor-400-ultrasonic-homogenizer.html
- https://ultrasonichomogenizer.com/
- https://homogenizers.net/pages/ac-ultrasonic-homogenization
- https://homogenizers.net/collections/sonic-homogenizers-sonicators
- https://www.hielscher.com/homogenize_01.htm
- Text Highlighting: Select any text in the post content to highlight it
- Text Annotation: Select text and add comments with annotations
- Comment Management: Edit or delete your own comments
- Highlight Management: Remove your own highlights
How to use: Simply select any text in the post content above, and you'll see annotation options. Login here or create an account to get started.