Combining a biological process with membrane filtration, a membrane bioreactor (MBR) wastewater treatment device separates particulates from treated water.
It combines microfiltration or ultrafiltration membranes retaining biomass and pollutants with an activated sludge process—where microorganisms break down organic pollutants.
MBRs successfully remove suspended particles, bacteria, and viruses by substituting membranes for traditional secondary clarifiers, therefore producing superior quality effluent.
Higher treatment efficiency and a more compact reactor design are made possible by running at increased mixed liquor suspended solids (MLSS) levels than by conventional systems.
With each design providing unique benefits in energy consumption and fouling control, MBRs may be set as submerged (immersed directly in the bioreactor) or sidestream (where wastewater is piped to an external membrane unit).
Although MBRs have greater initial capital and operating costs—mostly related to membrane fouling and cleaning needs—they minimize sludge generation and provide better nutrient removal, which appeals for water reuse and satisfies tight discharge criteria.
Particularly when space is limited and constant, high-quality effluent is vital, MBR technology’s adaptability makes it relevant in both municipal and industrial environments.
What is Membrane Bioreactor?
- Combining a biological treatment process with membrane filtration, a membrane bioreactor (MBR) is a wastewater treatment system.
- microbes in an MBR system break down organic materials in the wastewater, then the treated water is sent through a membrane filter to eliminate any last suspended particles and microbes. This produces a well processed effluent fit for either reusing or environmental disposal.
- Treating municipal and industrial wastewater as well as for water reuse uses MBR systems are very popular.
- The sewage effluent will be gathered in a chamber including a screen. This manually cleaned screen is used to eliminate free-floating, big particles that would otherwise choke pipe lines and pumps.
- Wastewater is gathered in an underground equalisation tank following screening and then blended using an air diffusion system. From the equalisation tank to the biological chamber, non-clogging submersible pumps move wastewater for further breakdown of organic contaminants.
- The Biological-MBR tank holds up to 8000 mg/l of MLSS, or mixed liquid suspended solids. The high bacterial concentration in a somewhat limited area helps to enable a more complete elimination of organic elements from raw sewage effluent.
- The oxygen the two-lobed air blower gives the microorganisms meets their need. The air is used oxygenating microorganisms as well as for cleaning membranes.
- A vacuum pump pulling penetration water straight from PMTR modules handles the filtering. The resultant permeate water boasts turbidity 1.0 NTU and is ultra-filtered.
- Membrane filtration is fundamental in water and wastewater treatment; its superior performance and cost-effectiveness make it better than more traditional water systems. Microfiltration, ultrafiltration, nanofiltration, and reverse osmosis are the core membrane processes (RO).
- MF ranges are 100 to 1000 nm; UF ranges are 5 to 100 nm; NF ranges are 1 to 5 nm; and RO ranges are 0.1 to 1 nm from these membranes. For almost ten years, MBRs—using membranes in the range of MF and UF—have been a practical secondary treatment solution.
- Mostly used for wastewater treatment (WWT), Membrane bioreactor (MBR) techniques combine microfiltration (MF) or ultrafiltration (UF) with a biological process such a suspended growth bioreactor. The created particles from the biological process are filtered using the membranes, therefore producing a product free of pathogens and clear. Figure shows an immersed MBR (iMBR) to offer a graphic representation.
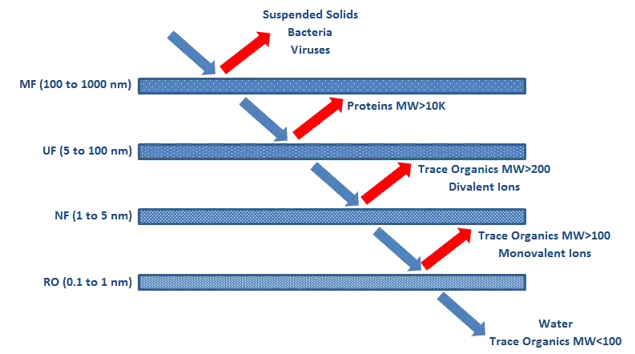
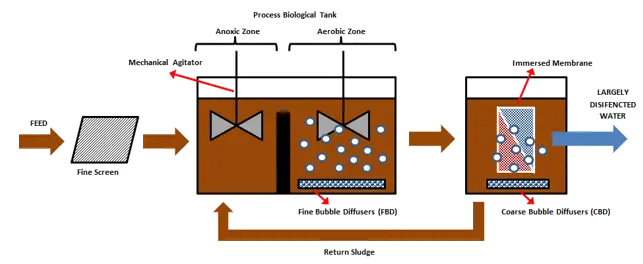
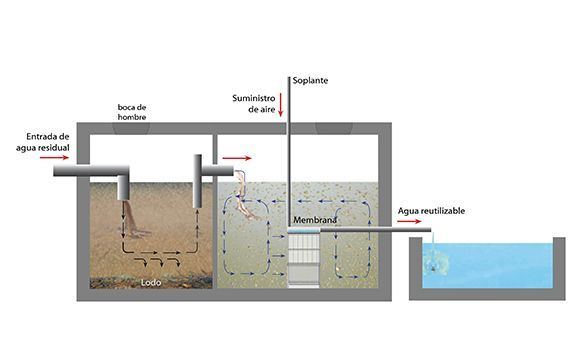
Working Principle of Membrane Bioreactor
- Combining the activated sludge process with a physical separation stage in one system, MBRs link membrane filtration and biological treatment.
- Wastewater combined with high quantities of activated sludge—where microorganisms break down organic contaminants and nutrients—is housed in a bioreactor tank.
- Aeration is brought in to provide turbulence that keeps the membrane surfaces free of foulants and to deliver oxygen for aerobic digestion.
- Following biological treatment, mixed liquor is sent to the membrane module where microfiltration or ultrafiltration membranes physically separate treated water (permeate) from suspended particles and biomass.
- Designed either as immersed (within the bioreactor) or sidestream (external to the reactor), the membranes serve as exact filters guaranteeing premium effluent.
- While obtaining excellent removal efficiency, operating at greater mixed liquor suspended particles levels enables a smaller reactor footprint.
- Transmembrane pressure is under constant observation as a rise indicates membrane fouling and the requirement of process modifications or cleaning.
- Generally speaking, an MBR’s operating concept produces less sludge, better effluent quality, and more operational flexibility than more typical secondary treatment systems.
Membranes
Solid–liquid separation is done by Microfiltration (MF) or Ultrafiltration (UF) membranes during MBR wastewater treatment. A membrane is merely a two-dimensional material that is typically used to separate fluid components based on their relative size or electrical charge. Semi-permeability is the capacity of a membrane to permit the passage of only particular molecules (sometimes also permselective). This is a physical process in which separated components remain unaltered chemically. Components that flow through the pores of a membrane are known as permeate, whereas those that are rejected create a concentrate or retentate.
There are 5 types of membrane configuration for MBRs:
- Hollow fibre (HF)
- Spiral-wound
- Plate-and-frame (i.e. flat sheet (FS))
- Pleated filter cartridge
- Tubular
Other topologies, such as spiral-wound (SW), are unsuitable for MBR applications due to their sensitivity to the presence of suspended particulates.
Parts of Membrane Bioreactors
A Membrane Bioreactor (MBR) system uses many critical components to efficiently treat wastewater:
- Pretreatment Unit: Screens, grit chambers, and oil/water separators remove big debris, heavy particles, and oil/grease from incoming wastewater, safeguarding succeeding components.
- In the biological reactor (aeration tank), microorganisms digest wastewater organic contaminants. Microbial activity and biomass suspension require oxygen from aeration systems.
- Membrane Module: Flat sheet, tubular, or hollow fiber membranes physically separate treated water from suspended particles and germs. Configure membranes as:
- Submerged (Immersed) Membranes:: Installed directly in the bioreactor or a separate tank, submerged membranes are above the aeration system, which delivers oxygen and cleans them.
- External (Sidestream) Membranes: Wastewater is pushed via external (Sidestream) membrane modules and returned to the bioreactor.
- Aeration System: The aeration system oxygenates the biological reactor, helping microorganisms break down organic materials. The aeration system creates turbulence to clean submerged membrane surfaces.
- Permeate Withdrawal System: This system captures membrane-filtered water (permeate) for treatment or disposal.
- Cleaning System: Periodic cleaning maintains membrane efficiency. Recirculating permeate across the membrane to eliminate fouling or chemical cleaning can remove accumulated pollutants.
Operating Procedure of Membrane Bioreactor
- First pretreatment for wastewater uses screens, grit chambers, and oil separators to remove significant trash and grit thereby safeguarding future operations.
- The pretreated water comes into the biological reactor and is combined with activated sludge; here, microorganisms employ aeration both to maintain the biomass in suspension and to provide oxygen for aerobic destruction of organic contaminants.
- By reusing some of the biomass and squandering extra sludge, the system maintains high mixed liquor suspended solids (MLSS) thereby enhancing the degrading efficiency and guaranteeing stable biological activity.
- Treated mixed liquor runs into the membrane module where either submerged (immersed in the bioreactor) or sidestream (external to the reactor) membranes microfiltration or ultrafiltration separates cleared water from suspended particles.
- While the retained biomass is recirculated into the reactor, constant removal of permeate produces high-quality effluent, therefore continuing the biological process and lowering total sludge generation.
- Closely monitoring transmembrane pressure (TMP), operators identify membrane fouling—which then sets off cleaning processes like backwashing or chemical cleaning to restore flux—by any notable increase.
- Real-time adjustments in key operating parameters—including hydraulic retention time (HRT), solids retention time (SRT), and food-to– microorganism (F/M) ratio—ensure best treatment performance and process stability.
- Comprehensive data logging of aeration rates, flux, and TMP facilitates planned maintenance and process changes, hence improving system efficiency and extending membrane lifetime.
- Planned shutdowns for regular membrane replacement and complete cleaning help to prevent long-term fouling and preserve constant high-quality effluent output.
Treatment Process
- First pretreatment of wastewater removes grit and big trash, therefore safeguarding the system from any harm and lowering the membrane fouling risk.
- The processed wastewater next passes into a biological reactor where it is combined with activated sludge; in this tank, microorganisms break down organic contaminants and change nutrients under aerobic conditions.
- Aeration inside the reactor generates turbulence keeping biomass in suspension and oxygen required for microbial metabolism at the same time, hence improving the degradation process.
- Maintaining high mixed liquid suspended solids (MLSS) and extended solids retention durations (SRT), guarantees strong biological activity, effective nutrient removal, and full nitrification.
- Microfiltration or ultrafiltration membranes separate clean water (permeate) from suspended particles and microbial biomass in the membrane module after the biologically treated mixed liquor is delivered there.
- While allowing treated water to flow through, the physical barrier of the membranes holds most of particulate matter and pathogens in the membrane filtering stage, hence producing excellent effluent quality.
- The retained biomass is recirculated back into the biological reactor while the permeate is collected for either discharge or reuse, hence optimizing efficiency in a continuous treatment loop.
- Key operating parameters like transmembrane pressure (TMP), flux, and aeration rates are continually watched throughout the process to identify and control membrane fouling, therefore triggering cleaning procedures when needed.
- Combining biological treatment with membrane separation inside one system produces a small, effective process that lowers sludge generation, improves nutrient removal, and produces high-quality effluent fit for either safe disposal or reuse.
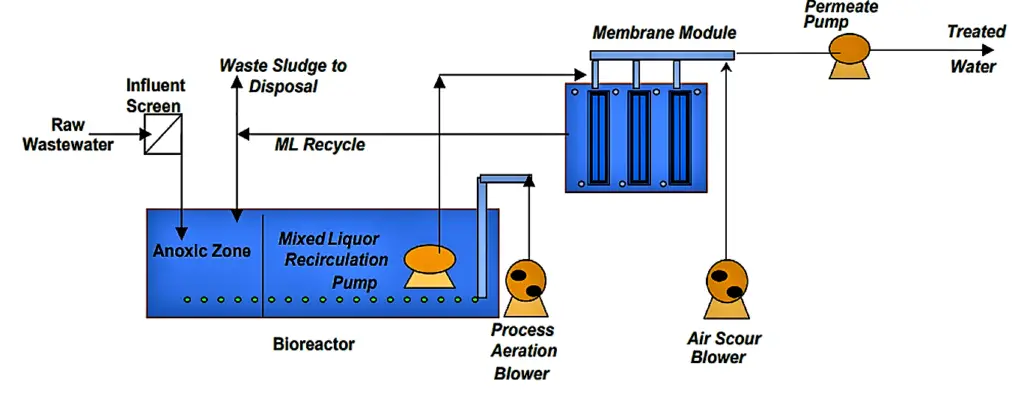
Types of Membrane Bioreactors
Advanced wastewater treatment systems use membrane bioreactors (MBRs) with biological degradation and membrane filtration. They are mostly grouped by system membrane module configuration:
- Submerged (Immersed) Membrane Bioreactors (SMBR):
- Configuration: SMBR membrane modules are immersed in biological treatment tanks.
Operation: Submerged membranes filter particles and biomass from wastewater after biological treatment, allowing permeate extraction. - Benefits: Lower transmembrane pressures mean less energy and a smaller footprint.
Aeration prevents membrane fouling and oxygenates microbes.
- Configuration: SMBR membrane modules are immersed in biological treatment tanks.
- External (Sidestream) Membrane Bioreactors (EMBR)
- Configuration: EMBR membrane modules are outside the biological reactor.
Pump biologically treated mixed liquid from the reactor to the external membrane unit for filtering. Retentate (concentrated biomass) is returned to the bioreactor. - Benefits: This design simplifies membrane maintenance and cleaning.
- Considerations: Pumping uses more energy than submerged systems.
- Configuration: EMBR membrane modules are outside the biological reactor.
1. Submerged Membrane Bioreactors (SMBR)
- Installed directly inside the biological reactor tank, a Submerged Membrane Bioreactor (SMBR) is a wastewater treatment system whereby the treatment and separation processes are integrated.
- Under aerobic circumstances, the biological reactor of an SMBR combines wastewater with high concentrations of activated sludge so that microorganisms break down organic contaminants and nutrients.
- Two functions of aeration in the reactor include providing oxygen for microbial breakdown and generating turbulence that constantly scours the submerged membranes to reduce fouling.
- Usually using microfiltration or ultrafiltration, the membranes of an SMBR let treated water—permeate—pass through while keeping biomass and suspended particles within the reactor.
- Operating at high mixed liquor suspended solids (MLSS) levels, SMBRs improve treatment efficiency and nutrient removal and also allow a compact reactor design with a reduced footprint.
- Maintaining an active microbial population and hence lowering the total generation of waste sludge, the system constantly recycles the retained biomass back into the reactor.
- Rising TMP signifies membrane fouling that requires regular cleaning, including backwashing or chemical cleaning, hence regular monitoring of transmembrane pressure (TMP) is absolutely vital.
- Combining biological degradation with membrane separation inside one, integrated unit, SMBRs provide an energy-efficient, space-saving, and high-performance solution for municipal and industrial wastewater treatment.
Operating Procedure of SMBR
- Starting pretreatment of the influent wastewater, the SMBR process removes significant particles and guards downstream components utilizing screens and grit chambers.
- Pre-treated water is supplied into the high concentration of activated sludge biological reactor tank where microorganisms break down organic contaminants.
- Aeration is constantly supplied to produce turbulence and deliver oxygen for microbial metabolism, therefore helping to minimize membrane fouling by scouring the submerged membranes.
- The high mixed liquid suspended solids (MLSS) kept in the reactor guarantees effective nutrient removal and strong biological activity.
- The submerged membrane modules in the reactor filter the treated mixed liquor; pure water (permeate) goes through while the biomass and suspended particles are retained.
- While the retained biomass is reintroduced back into the reactor to support the biological process, the permeate is taken constantly from the system.
- Real-time monitoring of transmembrane pressure (TMP) reveals any notable rises that point to membrane fouling triggering cleaning operations like chemical or backwashing.
- Regular adjustments to maximize performance and preserve process stability help key operational parameters—hydraulic retention time (HRT), solids retention time (SRT), and aeration rates—to be optimal.
- Data logging and regular maintenance support constant effluent quality and extend membrane life over lengthy running times.
Uses of Submerged Membrane Bioreactors (SMBR)
- SMBRs are mostly utilized for municipal wastewater treatment since their compact design and high biomass concentration remove organic matter, nutrients, and pathogens in a smaller footprint than traditional systems.
- SMBRs create high-quality effluent for reclamation, irrigation, and industrial process water, conserving freshwater.
- SMBRs are useful for updating existing treatment facilities because they can run at high mixed liquor suspended solids (MLSS) levels, increasing loading rates and effluent standards.
- Decentralized and small-scale wastewater treatment systems use SMBRs for reliable performance in urban or distant areas with limited acreage.
- SMBRs handle complicated wastewater streams with high organic loads or fluctuating pollutant profiles in industrial environments, maintaining constant performance and discharge compliance.
- Integrated process control and constant monitoring of crucial parameters like transmembrane pressure (TMP) help SMBRs manage membrane fouling effectively, ensuring system stability.
- SMBRs make good pre-treatment units for reverse osmosis, which requires high-quality feed water to protect downstream membranes and save energy.
Advantages of Submerged Membrane Bioreactors (SMBR)
- The combined biological degradation and membrane filtration of SMBRs reduces the need for extra settling tanks.
- The submerged design increases activated sludge concentrations, improving pollutant removal and nutrient degradation.
- SMBRs use less energy than external systems because they need lower transmembrane pressures.
- Aeration provides oxygen for microbial activities and reduces membrane fouling by creating turbulence.
- Small footprints make SMBRs ideal for urban or space-constrained installations for decentralized wastewater treatment.
- Retaining suspended particles and pathogens produces high-quality effluent for reuse or safe disposal.
- The system’s integrated process control and automation allow real-time parameter modifications, improving process stability and efficiency.
- Sludge reduction simplifies downstream handling and disposal, lowering costs and enhancing sustainability.
Limitations of Submerged Membrane Bioreactors (SMBR)
- Due of membrane and installation costs, SMBRs demand a considerable initial investment.
- Despite using less energy than sidestream systems, submerged membranes require regular aeration to prevent fouling, increasing operational expenses.
- SMBRs need periodic cleaning cycles, chemical cleaning, and membrane replacement due to membrane fouling.
- High mixed liquid suspended solids (MLSS) concentrations improve treatment efficiency but increase viscosity and fouling.
- The system’s success depends on careful management of operating parameters such aeration intensity, hydraulic retention time, and solids retention time.
- SMBRs may suffer with shock loads or influent quality changes, affecting effluent quality and process stability.
- Maintenance and downtime for membrane cleaning and replacement can lower system efficiency and raise long-term expenses.
2. External Membrane Bioreactors (EMBR)
- Sidestream MBRs, or external membrane bioreactors, place membrane modules outside the biological treatment tank rather than in the mixed liquor.
- THEMBRSITE.COM
- An EMBR system pumps wastewater to an external membrane unit for solid–liquid separation after microorganisms breakdown organic materials in a biological reactor.
- Microfiltration or ultrafiltration membranes separate high-quality permeate from biomass and suspended particles in the external unit.
- EMBRs isolate membranes from the bioreactor for easier maintenance and faster cleaning, minimizing membrane cleaning and replacement downtime.
- However, pumping mixed liquor to and from the exterior membrane module uses more energy than submerged systems.
- EMBRs are useful when maintenance is accessible or operating conditions allow optimum cleaning techniques to decrease fouling.
- This design is employed in industrial and municipal applications that need good effluent quality, despite its more complicated hydraulic setup and higher running expenses.
Operating Procedure of EMBR
- To remove big solids and safeguard downstream equipment, wastewater initially passes first treatment—screens, grit removal.
- The biological reactor receives the pretreated water and microorganisms break organic contaminants and nutrients there.
- Microfiltration or ultrafiltration membranes handle the separation as the treated mixed liquor is pushed from the biological reactor into the external membrane unit.
- The permeate—treated water—is split from the retained biomass and suspended particulates in the membrane unit.
- While the concentrated biomass is recirculated back into the biological reactor, the clear permeate is collected for either disposal or usage.
- Continually watched process metrics like hydraulic retention time, transmembrane pressure, and flux help to identify membrane fouling.
- Cleaning procedures such as backwashing or chemical cleaning start when an increase in transmembrane pressure is found to restore membrane function.
- By means of management of the hydraulic system, a steady flow between the biological reactor and the external membrane unit is guaranteed, therefore maximizing treatment efficiency and energy consumption.
Applications of EMBR
- Municipal wastewater treatment uses EMBRs to produce high-quality effluent for reuse.
- Industrial wastewater treatment uses them for high-strength or fluctuating waste streams.
- EMBRs aid water reclamation operations that require high-quality effluent.
- Decentralized systems that need modular, easy-to-maintain treatment units benefit from their design.
- To safeguard downstream systems, EMBRs can pretreat before reverse osmosis.
Advantages of EMBR
- EMBR membranes are outside the bioreactor, making backwashing and chemical cleaning easy.
- External design allows independent parameter control, thus filtering conditions may be tuned apart from biological treatment.
- EMBRs’ modular architecture allows membrane replacement and system scaling without disrupting therapy.
- Separating the membrane unit from the biological reactor reduces fouling since membranes are less exposed to biomass.
- Transmembrane pressure may be monitored better to improve effluent quality and process management.
- Circulating mixed liquor requires more pumping energy, but maintenance accessibility and operational flexibility generally outweigh this.
Disadvantages of EMBR
- Pumping mixed liquor raises energy and operational expenses in EMBRs.
- The external membrane unit’s piping and hydraulic controls increase system complexity and installation and maintenance costs.
- Separating the membrane from the biological reactor might increase footprint compared to immersed systems.
- System complexity may raise operating issues and maintenance downtime.
- Any mismatch between the reactor and external membrane unit might reduce treatment efficiency.
Other Types of Membrane Bioreactors
3. Hybrid Membrane Bioreactors (HMBR)
- In addition to membrane filtration, hybrid membrane bioreactors (HMBRs) combine suspended-growth (activated sludge) and attached-growth (biofilm) systems.
- The attached-growth component—often supported on media—increases microbial diversity and breaks down complex contaminants and removes nutrients.
- Combining suspended and fixed-film techniques lowers free-floating particulates and stabilizes biomass, reducing membrane fouling.
- HMBRs have lower food-to-microorganism ratios and longer solids retention durations, improving treatment efficiency and shock load robustness.
- Their small form and high-quality effluent make them excellent for municipal, industrial, and water reuse applications.
- HMBRs combine the benefits of biofilm systems with standard MBRs, balancing process stability, pollutant removal, and operational flexibility.
Applications of HMBR
- Municipal wastewater treatment uses HMBRs to create high-quality effluent for reuse or safe release.
- Combining suspended and attached growth techniques treats variable-load industrial wastewaters.
- HMBRs improve nutrient removal and membrane fouling for water reclamation.
- They work well in decentralized, small-scale systems that need process consistency and space efficiency.
- Advanced nitrification, denitrification, and phosphorus removal are possible with their integrated design.
Advantages of HMBR
- Improves complicated pollutant degradation with suspended and attached growth.
- Stabilizing biomass with biofilms reduces membrane fouling.
- Increases nutrient removal and treatment efficiency.
- Increases process stability and load resilience.
- Compact design reduces sludge generation and running expenses.
Disadvantages of HMBR
- Integrating two treatments complicates systems.
- Higher capital and operational expenditures may be needed.
- Biofilm medium requires extra care.
- Microbial populations are difficult to balance.
- Insufficient field experience might hinder scaling.
4. Integrated Membrane Bioreactors (IMBR)
- Integrated Membrane Bioreactors (IMBRs) unite membrane filtration with the biological treatment process into one single device.
- They combine extra treatment phases—such as polishing, disinfection, or pre-treatment—into a small, simple package.
- IMBRs are meant to maximize process efficiency, raise effluent quality, and lower the total wastewater treatment plant footprint.
- Better control of operating parameters made possible by the integrated design increases nutrient removal and reduces sludge generation.
- IMBRs have operational benefits, but their complexity in combining several systems calls for exact design and management.
Uses of IMBR
- Municipal wastewater treatment with IMBRs produces high-quality effluent.
- They favor water reuse and reclamation.
- Industrial wastewater treatment uses IMBRs for improved polishing.
- Their small, integrated design suits dispersed systems.
- They combine biological therapy and polishing in one step.
Advantages of IMBR
- Combining membrane filtration and biological therapy into one small device
- improves effluent quality by including polishing actions.
- Minues space needs and plant footprint
- enhances operational efficiency and management of processes.
- reduces long-term running expenses and sludge output.
Disadvantages of IMBR
- Complex integrated design raises capital and operational expenses.
- Multiple therapy components increase maintenance issues.
- Possible membrane fouling affecting system performance
- Reduced flexibility for modifying individual treatment stages
- Required professional operation and rigorous process control for maximum efficiency.
5. Membrane Aerated Biofilm Reactor (MABR)
- The MABR wastewater treatment method supplies oxygen straight to a biofilm developing on the membrane surface by use of gas-permeable membranes.
- While generating gradients that allow simultaneous nitrification in the oxygen-rich outer layer and denitrification in the anoxic interior zones, oxygen diffuses across the membrane promoting aerobic microbial activity in the biofilm.
- Compared to conventional aeration, the design improves oxygen transfer efficiency, therefore reduces energy consumption and operating expenses.
- Effective for both municipal and industrial wastewater treatment, MABRs promote a regulated biofilm environment, therefore facilitating increased nitrogen removal.
- Reduced sludge generation, better treatment performance, and simpler integration with current wastewater infrastructure follow from the reactor’s small size and focused oxygen delivery.
Uses of MABR
- Municipal wastewater treatment uses MABRs to remove nitrogen.
- Decentralized and small wastewater treatment systems are supported.
- MABRs are used in industry for energy-efficient treatment.
- High-quality effluent for water reuse and reclamation projects is available.
- For lower aeration energy costs and better process control, MABRs are excellent.
Advantages of MABR
- MABRs improve oxygen transmission by delivering oxygen directly via membranes.
- They minimize mechanical aeration to save energy.
- The technology develops biofilm zones for simultaneous nitrification and denitrification.
- MABRs fit in tight spaces due to their compact form.
- Process management improves effluent quality and reduces sludge.
Disadvantages of MABR
- High initial capital expenses owing to sophisticated membrane materials and system design.
- Membrane fouling and clogging still hinder performance.
- Precision and ability are needed to maintain biofilm thickness.
- Wastewater quality might affect the process.
- Limited full-scale operational data makes long-term performance unpredictable.
6. Moving Bed Bioreactor (MBBR)
- A Moving Bed Bioreactor (MBBR) is a method of treating wastewater whereby biofilm development is supported by free-floating plastic carriers.
- Because the carriers give microbes a lot of surface area, they may effectively adhere and break down nutrients and organic debris.
- The biofilm-coated carriers in an MBBR system move constantly with the wastewater to improve mass transfer and treatment efficacy.
- Combining the advantages of suspended and connected growing systems, this technique has a small design and reduced sludge generation.
- For organic removal and nutrient (nitrogen and phosphorus) reduction in municipal and industrial wastewater treatment, MBBRs find extensive use.
Applications of MBBR
- Used to remove organics and nutrients from municipal wastewater.
- Used in industrial wastewater treatment to handle strong waste
- Suitable for dispersed and small-scale installations
- Used to upgrade traditional treatment plants
- Helps water reuse projects
Advantages of MBBR
- High carrier surface area promotes biofilm formation.
- Works well under shock and changing loads
- The compact form makes retrofitting existing plants straightforward.
- Low sludge output cuts disposal and handling expenses.
- High process robustness and flexibility with simple operation
Disadvantages of MBBR
- Keeping carriers moving requires strong mixing energy.
- Carrier biofilm can limit mass transfer efficiency.
- Carriers may wear out and need replacement.
- Without optimization, colder regions may lower performance.
- Limited biofilm thickness management might cause operational issues.
Each type of MBR has its own advantages and disadvantages, and the best choice will depend on the specific treatment goals and the characteristics of the wastewater.
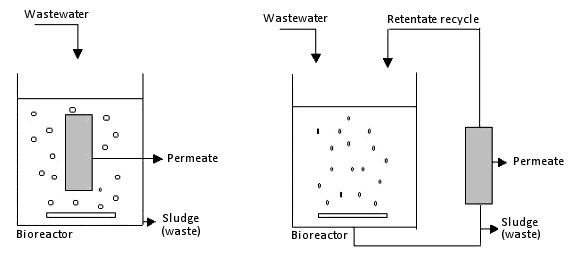
Membrane bioreactor design
- The concept combines membrane filtration with biological treatment into a small device that effectively treats wastewater.
- Pretreatment facilities (screens, grit chambers) start it in order to eliminate big solids and guard downstream components.
- Designed to sustain high mixed liquid suspended solids (MLSS) for efficient pollution degradation, the biological reactor is
- To balance energy usage and fouling management, membrane modules are chosen according to type—hollow fiber, flat sheet, or tubular—and configuration—submerged or sidestream.
- Aeration systems are used to provide oxygen and produce turbulence that reduces membrane fouling.
- Optimized for performance are key operating parameters include hydraulic retention time, solids retention time, flux, and transmembrane pressure.
- For reasonably priced operation, the general design takes footprint, energy consumption, and maintenance comfort of mind into account.
- Integrated advanced monitoring and control systems let conditions be changed in real time to guarantee constant effluent quality.
- Scalability and adaptability made possible by modular architecture enable one to refit or expand as treatment requirements change.
Design Features
- Higher biomass concentrations and better effluent quality are made possible by MBR systems combining a suspended growth bioreactor with a membrane filtering unit to replace traditional secondary clarifiers.
- Systems may utilize immersed (submerged) configurations, where membranes function inside the bioreactor, or sidestream setups with separate membrane tanks, each providing various trade-offs in energy usage and ease of maintenance; the choice of membrane configuration is therefore crucial.
- Materials such PVDF or ceramic are chosen according on required pore size, chemical resistance, and long-term durability under cleaning conditions from among hollow fiber, flat sheet, or tubular geometries.
- Important operational characteristics include permeate flow, transmembrane pressure (TMP), and membrane permeability; thus, management of fouling and preservation of stable performance depend on appropriate aeration and process design to regulate these aspects.
- Protection of membranes from physical damage and lowering of fouling potential depends on a strong pretreatment stage involving coarse and fine screening, grit removal, and sometimes primary clarifying.
- Usually in the range of 4,000 to 15,000 mg/L, the bioreactor design must preserve high mixed liquor suspended solids (MLSS) concentrations to ensure successful biodegradation while permitting separate regulation of hydraulic and solids retention durations.
- Aeration design has two purposes: it provides oxygen for microbial metabolism and generates shear forces (air scouring) to remove foulants from the membrane surface; thus, optimal bubble size and distribution are very vital for effective operation.
- Including system redundancy—that is, designing with extra membrane units—N+1 configurations—ensures continued treatment capacity even during cleaning or maintenance cycles.
- Using PLC systems with automated cleaning processes helps to integrate modern process controls, therefore enabling real-time monitoring of important parameters and reducing operator involvement for maximum dependability.
- MBR technology is flexible for municipal, industrial, and distributed wastewater treatment uses because overall design factors balance treatment performance, energy consumption, capital and operational costs, and footprint limits.
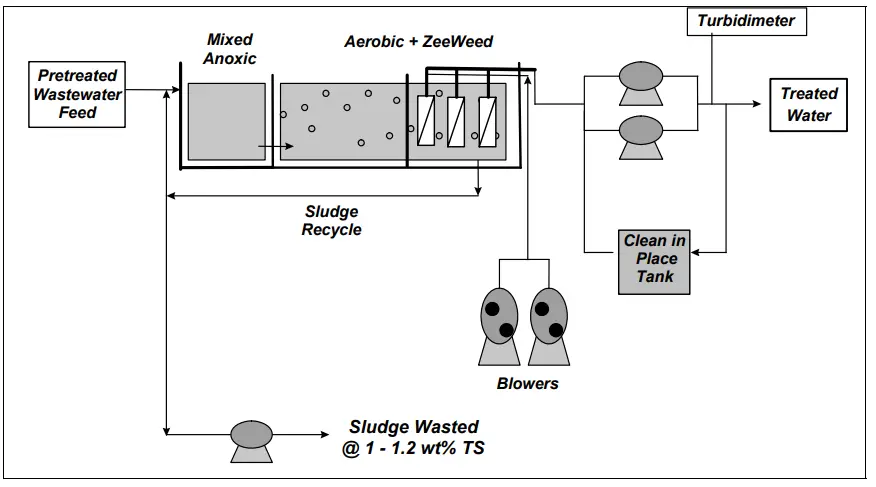
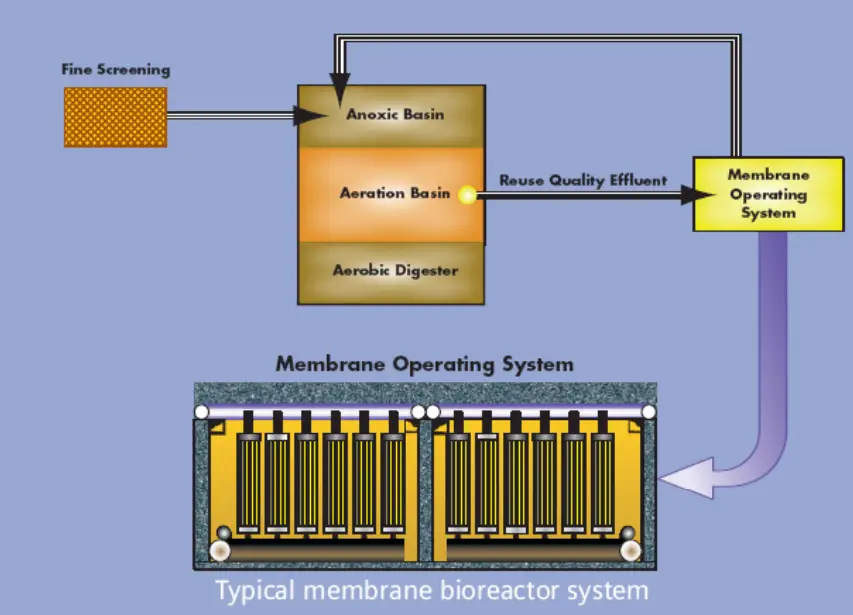
Membrane fouling control and cleaning
- Membrane fouling in MBRs is the collection of suspended particles, colloids, and biofilm on the membrane surface that reduces permeate flow and raises transmembrane pressure.
- Strong pretreatment—using fine screening, grit removal, and, where needed, primary clarification—helps to lower the particle and fiber load that speeds membrane fouling.
- Aeration is essential in submerged MBR setups; tiny bubble air scouring generates shear forces over the membrane surface, physically dislodges accumulated foulants, and preserves steady flow.
- Backwashing and intermittent filtration—relaxation cycles—allow foulants to drift away from the membrane, therefore lowering the rate of irreversible fouling and increasing the lifetime of the membrane.
- Transmembrane pressure (TMP) must be constantly monitored; a slow TMP rise acts as an early signal for fouling development, therefore guiding the early start of cleaning cycles.
- In line with manufacturer guidelines, chemical cleaning methods utilizing chemicals such as sodium hypochlorite and citric acid are used when physical cleaning approaches are unable to remove difficult organic and inorganic deposits.
- Modern methods, like back-pulsing—where some of the permeate is briefly reversed across the membrane—help remove pore blockages and reduce the need for repeated chemical treatments.
- Choosing membrane materials with naturally low fouling tendencies—that is, those with smooth surfaces or anti-fouling coatings—and improving module design would greatly lower cleaning frequency and total running expenses.
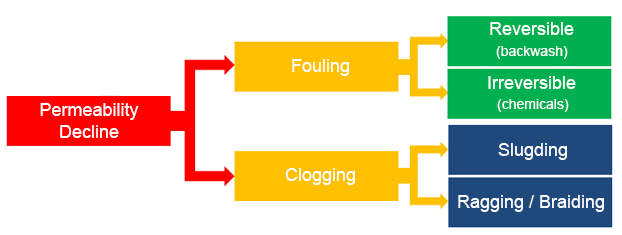
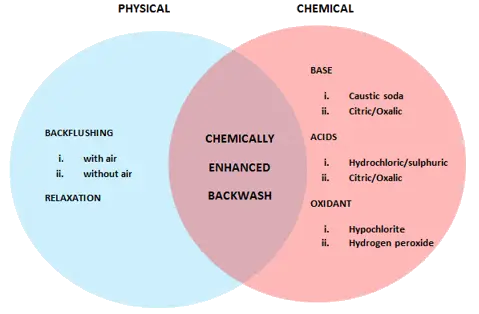
Applications of Membrane Bioreactors
- Municipal wastewater treatment with MBRs produces high-quality effluent with minimal suspended particles and pathogens, making it ideal for urban irrigation, industrial operations, and potable water augmentation.
- Due to its capacity to manage changing loads and remove resistant organic compounds, MBR systems are used in food and beverage, pharmaceutical, textile, and petrochemical industries to treat complex or high-strength wastewaters.
- MBR installations help decentralized and distant populations by providing effective wastewater treatment in areas where traditional systems are impracticable or too large.
- Water reclamation projects employ MBR technology to recycle municipal or industrial wastewater for toilet flushing, landscaping, and industrial process water, lowering freshwater demand.
- In ecologically sensitive areas with tight discharge criteria, MBRs remove nutrients and pathogens to comply with regulations and safeguard receiving water bodies.
- Integration with anaerobic processes for energy recovery from wastewater is emerging. Anaerobic MBRs create biogas while treating wastewater, which can provide on-site electricity and minimize operational costs.
- MBR systems are also being tested for treating landfill leachate and other difficult waste streams, indicating its adaptability and potential for wider deployment in different environmental circumstances.
Advantages of Membrane Bioreactors
- Effective suspended particles and pathogen removal produces high-quality effluent.
- High biomass concentration and small plant footprint are possible with compact design.
- Controlling hydraulic and solids retention times separately stabilizes processes.
- Low sludge generation cuts disposal costs and complexity.
- Clean effluent increases water reuse possibilities.
- Operational flexibility allows stable performance under fluctuating load.
Disadvantages of Membrane Bioreactors
- High capital and operational expenses compared to traditional systems
- Periodic membrane fouling requires cleaning and maintenance.
- Intensive aeration and pumping need energy.
- Specialist control and skill needed for complex operation
- Limited peak flow flexibility may need more capacity.
Advantages | Disadvantages |
Compact | Aeration limitations |
High effluent quality | Stress on sludge in external MBR |
High volumetric load possible | Membrane pollution |
High rate of degradation | Cost price |
Possible to convert from existing conventional active sludge purification |
Comparison of External and Internal Membrane Based MBR System Configurations
Comparative Factor | External MBR Systems | Internal MBR Systems |
Membrane Area Requirement | Characterized by higher flux and therefore lower membrane area requirement. | Lower flux but higher membrane packing density (i.e., membrane area per unit volume) |
Space or Footprint Requirements | Higher flux membranes with bioreactor operating at higher VSS concentration and skidded assembly construction, results in compact system. | Higher membrane packing density and operation at bioreactor VSS concentration of 10 g/l or greater translates to compact system. |
Bioreactor and Membrane Component Design and operation Dependency | Bioreactor can be designed and operated under optimal conditions including those to achieve biological N and P removal, if required. | Design and operation of bioreactor and membrane compartment or tank are not independent. High membrane tank recycle required (e.g., recycle ratio 4) to limit tank VSS concentration build-up |
Membrane Performance Consistency | Less susceptible to changing wastewater and biomass characteristics. | More susceptible to changing wastewater and biomass characteristics requiring alteration in membrane cleaning strategy and/or cleaning frequency |
Recovery of Membrane performance | Off-line cleaning required every 1 to 2 months. Simple, automated procedure normally requiring less than 4 hours. | Off-line “recovery” cleaning required every 2 to 6 months. A more complex procedure requiring significantly more time and manual activity, at least on occasion may be required (i.e., physical membrane cleaning). |
Membrane Life or Replacement Requirements | Results to-date implies an operating life of 7 years or more can be achieved with polymeric prior to irreversible fouling. Operating life of ceramics much longer | Results to-date implies an operating life of 5 years may be possible prior to irreversible fouling and/or excessive membrane physical damage. |
Full Scale Application Status | Conventional membrane based systems have a very long track record. Few non-conventional systems in operation in the U.S. | Full scale application widespread in the U.S. |
Economics | Non-conventional designs translate to comparable power costs. Comparable capital cost at least at lower wastewater feed rates (e.g., approaching 1893 m3/day). | Power and capital cost advantage at higher wastewater feed rates. |
- Pandey, Aditi & Singh, Ravi. (2014). Industrial Waste Water Treatment by Membrane Bioreactor System. Elixir Chemical Engineering. 70. 23772-23777.
- Iorhemen OT, Hamza RA, Tay JH. Membrane Bioreactor (MBR) Technology for Wastewater Treatment and Reclamation: Membrane Fouling. Membranes (Basel). 2016 Jun 15;6(2):33. doi: 10.3390/membranes6020033. PMID: 27314394; PMCID: PMC4931528.
- Nagy, E. (2019). Membrane Bioreactor. Basic Equations of Mass Transport Through a Membrane Layer, 381–415. doi:10.1016/b978-0-12-813722-2.00014-5
- Galinha, C. F., Sanches, S., & Crespo, J. G. (2018). Membrane bioreactors. Fundamental Modelling of Membrane Systems, 209–249. doi:10.1016/b978-0-12-813483-2.00006-x
- Al-Asheh, S., Bagheri, M., & Aidan, A. (2021). Membrane bioreactor for wastewater treatment: A review. Case Studies in Chemical and Environmental Engineering, 4, 100109. doi:10.1016/j.cscee.2021.100109
- https://www.lenntech.com/processes/mbr-introduction.htm
- https://emis.vito.be/en/bat/tools-overview/sheets/membrane-bioreactor
- http://www.amtaorg.com/Membrane_Bioreactors_for_Wastewater_Treatment.html
- https://sswm.info/water-nutrient-cycle/wastewater-treatment/hardwares/semi-centralised-wastewater-treatments/membrane-bioreactor
- https://www.pcimembranes.com/articles/membrane-bioreactors-mbr-for-wastewater-treatment/
- https://www.hyperfilteration.in/membrane-bioreactor.html
- https://encyclopedia.pub/entry/2622
- https://www.marketsandmarkets.com/Market-Reports/membrane-bioreactor-market-484.html
- https://www.directindustry.com/industrial-manufacturer/membrane-bioreactor-83997.html
- https://wtp-operators.thewaternetwork.com/article-FfV/membrane-bioreactor-advantages-GB3Q_UKmua4tsz-VTcs_1A
- https://research-advances.org/index.php/IRAJTE/article/view/920
- https://samcotech.com/technologies/biological/membrane-bioreactor-mbr/
- https://www.bioazul.com/en/technologies-and-products/mbr-membrane-bioreactor/
- https://www.ecologixsystems.com/library-mbr/
- https://www.thembrsite.com/membrane-bioreactor-basics/what-are-mbrs/
- https://www.kubota.com/products/johkasou/technology/membrane_biorector.html
- https://www.epa.gov/sites/default/files/2019-08/documents/membrane_bioreactor_fact_sheet_p100il7g.pdf
- Text Highlighting: Select any text in the post content to highlight it
- Text Annotation: Select text and add comments with annotations
- Comment Management: Edit or delete your own comments
- Highlight Management: Remove your own highlights
How to use: Simply select any text in the post content above, and you'll see annotation options. Login here or create an account to get started.