What is Centrifugal Separators?
- Centrifugal separators are mechanical devices that use the force generated by rapid rotation to separate mixture components based on differences in density
- They operate by spinning a container or bowl at high speeds so that denser substances are forced outward while lighter substances remain closer to the center
- The underlying principle is described by the relationship F₍c₎ = m · r · ω², where m represents mass, r is the radius, and ω is the angular velocity
- Historically, early forms of centrifugal separation were used in the dairy industry to separate cream from milk by allowing the heavier milk to be pushed outward, leaving the lighter cream to collect near the center
- Gustaf de Laval’s innovations in the late nineteenth century led to the development of the first commercially practical cream separators, which transformed dairy processing
- Over time, centrifugal separators evolved from manually operated devices to highly automated systems featuring self-cleaning mechanisms and advanced control technologies
- Modern centrifugal separators are used across multiple industries, including dairy processing, wastewater treatment, chemical manufacturing, oil refining, and pharmaceutical production
- In industrial settings, these separators are integral to clarifying liquids, dewatering sludges, and recovering valuable materials by efficiently segregating solids from liquids
- In nuclear technology, gas centrifuges are employed for isotope separation, notably in uranium enrichment, due to their high efficiency and reduced energy consumption
- Laboratory ultracentrifuges play a crucial role in biological and chemical research by isolating cellular organelles, proteins, and nucleic acids with high precision
- Advances in materials and design have enhanced the efficiency, reliability, and ease of maintenance of modern centrifugal separators, ensuring continuous process integration in diverse applications
- The evolution of centrifugal separation technology illustrates the successful application of physics, engineering, and material science principles to solve complex industrial separation challenges
Working Principle of Centrifugal Separator
- Operating by submitting a mixture to high-speed spinning generating centrifugal force, centrifugal separators cause heavier particles or droplets to migrate radially outward while lighter components remain near the axis of rotation.
- The separation process depends on the idea that the sedimentation of denser phases is enhanced by the rise of the centrifugal force with both the angular velocity squared and the radial distance.
- Different densities induce a fast stratification as the mixture moves inside the spinning chamber, wherein heavier materials are pushed to the perimeter and are constantly evacuated while lighter fluids build up in the middle area.
- Usually, the design uses a spinning bowl or disc stack to provide continuous operation by allowing the separated components to be moved under control toward specified outputs.
- Optimizing the separation efficiency depends critically on key operating factors including rotating speed, feed rate, and temperature as these influence the degree of the centrifugal force and particle settling velocity.
- The fundamental process is closely connected to Stokes’ equation, which explains the settling velocity of particles in a fluid and is suited to account for the enhanced acceleration due to rotation, therefore giving a quantitative basis for system design and analysis.
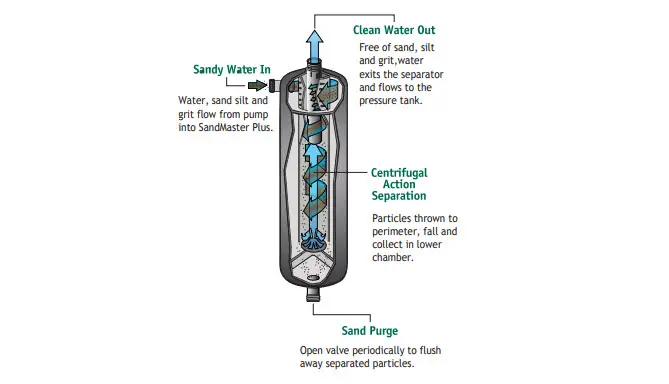
What Can a Centrifugal Separator Separate?
- Effective for separating heavier particles from lighter ones, centrifugal separators distinguish components depending on density.
- They are often used to separate solids from liquids, including cleaning water of suspended particles or silt.
- In industrial and environmental contexts, they may separate immiscible liquids, like oil from water.
- They are used in the food business to separate cream from milk, therefore highlighting their part in dairy processing.
- Essential in pharmaceutical and chemical production, they help liquids to be purified by eliminating tiny particles.
- They also help to separate stable emulsions into separate phases, therefore improving product quality and recovery.
- Although liquid-solid and liquid-liquid separations remain the major emphasis, in some specific applications they may conduct gas-liquid separations.
- Their adaptability makes them essential in big-scale industrial operations as well as in laboratory research.
Instrumentation/Parts of Centrifugal Separators
Centrifugal separators have these major parts:
- Feed pipe: The separator receives mixture through the feed pipe.
- Rotor: This core component rotates at high speeds to provide centrifugal force to separate substances.
- Drive mechanism: This component spins the rotor. A gas engine, electric motor, or other power source may be used.
- Bowl: Container for separating mixture. Metal or a robust composite is usually used.
- Separation chamber: The bowl’s separation chamber.
- Outlet pipe: The separator discharges chemicals through this pipe.
- Scraper: The scraper removes separated material from the bowl or separation chamber.
- Control panel: The operator may regulate the rotor speed and check separator performance using this component.
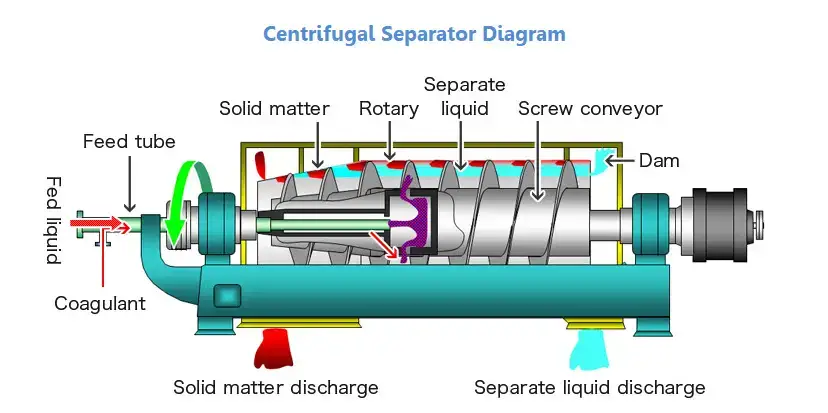
Types of Centrifugal Separators
- Decanter Centrifuges: Use a horizontal spinning bowl to separate high-solid-content slurries into liquid and solid phases; often used in wastewater treatment and sludge dewatering.
- Disc Stack Centrifuges: Often used in the dairy sector for cream separation and beverage clarifying, these centrifuges employ a series of conical discs to improve the separation of immiscible liquids and fine particles.
- Tubular Bowl Centrifuges: These centrifuges employ a basic cylindrical bowl shape to separate fine particulates from liquids and are commonly used in pharmaceutical applications to purify biological products.
- Hydrocyclones: Used in mineral processing and oil production for solid-liquid separations, they produce a vortex with a stationary conical vessel.
- Disc Separators: Utilize stacked discs to create strong centrifugal forces that make it easier to separate solids from various liquid stages. These separators are useful in biotechnology and food processing industries.
- Scroll Separators: Used in chemical and environmental engineering to handle mixtures with different solid contents.
- Clarifiers: Designed to remove tiny particles from liquids, increasing clarity and purity; used in beverage manufacturing and wastewater treatment to produce high-quality effluent.
- Purifiers: Used to separate two immiscible liquids and any entrained solids, such as oil and water mixes, which is vital in maritime and industrial applications for fuel purification and oil recovery.
Operating Procedure of Centrifugal Separators
- Examine the installation site to make sure all safety precautions are in place and the equipment is firmly attached.
- Make that the control panel, feed system, and discharge outlets—among other instruments—are calibrated and in working order.
- Starting a startup by running the control system and progressively raising the motor speed to the required operating level
- Through the specified feed line, gradually introduce the feed mixture to attain a homogeneous distribution inside the spinning chamber.
- Watch the stratification process as centrifugal forces split the liquid into many strata depending on density variations.
- Reversing operating parameters like feed rate, rotating speed, and temperature in reaction to real-time performance data can maximize separation efficiency.
- Fine-tuning the outlet settings helps direct separated components into their proper discharge channels, therefore preventing remixing.
- Track the system constantly on the control panel for any deviations or abnormalities; make required changes to preserve best performance.
- Finish the process by progressively lowering the rotating speed and stopping the feed so the machine may safely slow down.
- Plan regular maintenance to guarantee long-term dependability; post-operation checks and cleaning help to eliminate any remaining contaminants.
Uses of Centrifugal Separator
- Wastewater treatment makes extensive use of centrifugal separators to help sludge dewatering and remove suspended particles.
- Their effective separation of cream from milk improves product consistency and is therefore very important in the dairy sector.
- They are used in food and beverage production to eliminate particle pollutants and clarify liquids, therefore guaranteeing high-quality output.
- These separators help the biotechnology and pharmaceutical industries precisely separate active chemicals and clean biological samples.
- Centrifugal separators help to separate immiscible liquids and reaction byproducts in chemical processing, therefore maximizing process efficiency.
- These tools help the oil and gas sector separate oil, water, and other pollutants, thereby improving the refining and recycling techniques.
- In environmental remedial projects, where they assist to eliminate contaminants from industrial effluents and contaminated water, they are very vital.
- Centrifugal separators help mining activities by separating priceless mineral particles from slurry mixes, therefore enhancing resource recovery.
- Small-scale centrifugal separators are used in laboratory research for sample analysis, therefore allowing exact component separation for different tests.
Advantages of Centrifugal Separators
- Through fast acceleration of the sedimentation process under high centrifugal forces, centrifugal separators produce improved separation efficiency.
- In industrial environments, they provide constant throughput and reduce operational disruptions by helping continuous processing.
- Their small size allows great performance within restricted area, which qualifies for installations with spatial restrictions.
- Perfect tuning of the separation process depends on the capacity to precisely manage operational parameters like rotating speed and feed rate.
- They efficiently handle both liquid-solid and liquid-liquid separations with great flexibility, thereby allowing a wide spectrum of feed kinds.
- Reducing the dependence on gravity-based separation techniques helps to achieve energy efficiency and thereby decrease general running expenses.
- Reliable performance and low maintenance needs are achieved in part by robust building and automated control systems.
- Scalability in laboratory and industrial uses guarantees that centrifugal separators stay flexible for different production volumes and research requirements.
Limitations of Centrifugal Separators
- Because they depend on high-speed motors and energy-intensive operations, centrifugal separators usually demand substantial initial investment and incur large running expenses.
- Their performance is quite susceptible to feed composition changes like irregular flow rates, particle sizes, or density fluctuations that could lower separation efficiency.
- Because of constant high-speed rotation and mechanical stresses, the equipment is prone to wear and tear; so, regular maintenance and specific repairs are necessary.
- Their limited applicability in some mixes stems from their poorer efficiency in separating components with extremely comparable densities or when the density variations between phases are small.
- High-viscosity or abrasive fluids might slow down separation performance and hasten internal component deterioration, therefore lowering the device’s lifetime.
- Operating noise and vibration might present environmental and operational difficulties that call for more structural support and dampening techniques.
- Certain designs, notably disc-stack centrifuges, have restricted solids content they can handle and may suffer from clogging or obstruction should feed pre-treatment be insufficient.
- The intricate design and sensitivity to operating factors might call for strict process control and pre-treatment actions, therefore raising the general process complexity and expense.
Areas of Application of Centrifugal Separators
- In wastewater treatment, centrifugal separators are used widely to remove suspended materials and dewater sludge, therefore improving water quality before discharge or reuse.
- In the dairy sector, they are crucial for separating cream from milk and clarifying liquid goods, therefore improving product consistency and cutting processing times.
- These devices are used in oil and gas production to remove oil, water, and other pollutants from generated fluids therefore guaranteeing cleaner process streams and avoiding downstream equipment fouling.
- Centrifugal separators help solvents be purified, active substances be isolated, and tiny particles be removed from reaction mixes in chemical and pharmaceutical operations.
- By removing pollutants from contaminated water and allowing the recovery of valuable resources from waste streams, they are very vital in environmental remedial efforts.
- Centrifugal separators effectively separate precious mineral particles from slurry mixes, hence improving resource recovery in mining and mineral processing.
- Small-scale centrifugal systems for exact sample preparation, analysis of biological fluids, and separation of particle matter in many scientific studies help laboratory research and development.
- These separators are used in biotechnology and bio-processing applications to harvest cells, clear fermentation broths, and minimally disruptably purify biomolecules.
Tips to Improve the Efficiency of Centrifugal Separators
- To reduce wear and preserve consistent performance, routinely calibrate and maintain moving components including rotors, seals, and purging systems.
- To guarantee enough residence time for efficient separation, match the particle size and density of the feed to the capacity of the separator.
- To strike a compromise between strong centrifugal force and regulated energy consumption, change operational parameters including rotational speed and differential speed.
- Use sedimentation tanks or mesh screens to filter large particles that can clog the system and lower performance.
- Track flow rates, pressure, and separation quality automatically using real-time monitoring systems to support quick changes and predictive maintenance.
- To stabilize internal pressures, fine-tune valve settings and back-pressure controls, therefore improving phase separation and reducing energy loss.
- To catch smaller particles and raise general separation efficiency, think about adding extra stages such polishing or coalescing units.
- Comprehensive operator training will help to guarantee correct starting, troubleshooting, and adherence to maintenance plans, therefore preventing downtime and optimizing performance.
- Text Highlighting: Select any text in the post content to highlight it
- Text Annotation: Select text and add comments with annotations
- Comment Management: Edit or delete your own comments
- Highlight Management: Remove your own highlights
How to use: Simply select any text in the post content above, and you'll see annotation options. Login here or create an account to get started.