What is Wave Bioreactor?
- Designed as specialized bioprocess systems, wave bioreactors gently, wave-like mixing in disposable culture bags by means of a rocking action.
- The bioreactor is tilted on the rocking platform to create continuous waves that guarantee proper distribution of nutrients and oxygen across the cell culture media.
- This kind of agitation reduces shear stress on delicate cells relative to conventional stirred-tank bioreactors, therefore encouraging better cell development.
- They are extensively used in biopharmaceutical production including monoclonal antibody synthesis, recombinant protein expression, and vaccine manufacture.
- The design of the disposable bag lowers contamination risk and shortens cleaning and validation periods, therefore complementing contemporary cGMP guidelines.
- Because wave bioreactors are scalable, process consistency is maintained even when small-scale research projects are smoothly transitioned to large-scale commercial manufacture.
- Crucially for maximizing cell production and viability is exact control over important factors including temperature, pH, and dissolved oxygen.
- The technology is developing to combine real-time monitoring and automation, therefore providing improved process control and efficiency in bioprocessing operations.
- All things considered, wave bioreactors provide a strong and reasonably priced way to grow cells under circumstances that maximize output and quality of products.
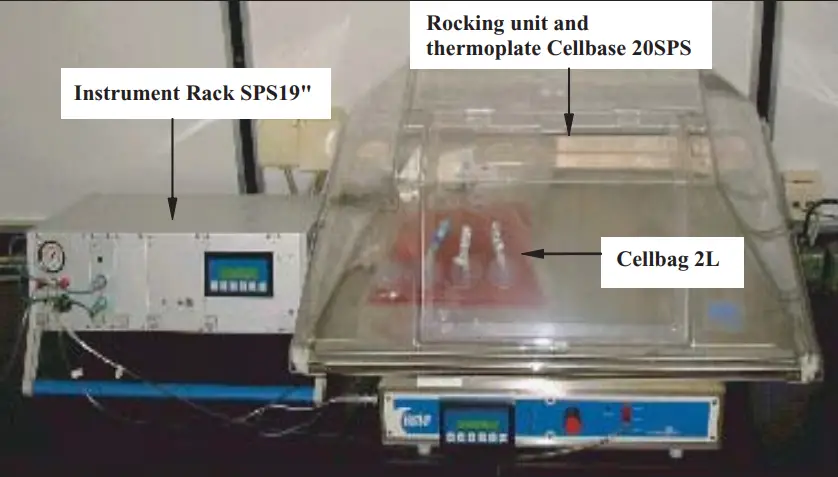
Working Principle of Wave Bioreactor
- Using a disposable culture bag set on a rocking platform, wave bioreactors provide mild, wave-like vibrations to stir the cell culture liquid and cells.
- The regulated rocking action tilts the platform at a specified frequency and angle to guarantee periodic renewal of the whole cultural volume for consistent distribution of nutrients and oxygen.
- Perfect for developing fragile cell lines and delicate bioprocesses, the wave-induced agitation reduces shear stress unlike conventional stirred systems.
- One of the main innovations is the disposable cellbag, which simplifies general process validation and turnaround times, removes cleaning and sterilizing processes, and lowers contamination concerns.
- Integrated sensors track important variables including temperature, pH, and dissolved oxygen, allowing exact changes to keep ideal conditions.
- Apart from improving mixing, the mild wave motion guarantees constant oxygenation over the culture media and helps effective gas transport by avoiding bubble development.
- Its architecture helps scalability, allowing researchers to keep repeatable culture settings while moving from small-scale studies to large-scale commercial production.
- Particularly in uses like vaccine production and recombinant protein synthesis, the simplicity and low capital investment of the system appeal for research and biopharmaceutical manufacture.
- Through careful adjustment of factors such rocking speed, amplitude, and gas flow, operators may match the bioreactor to the particular requirements of various cell types, hence improving cell viability and product quality.
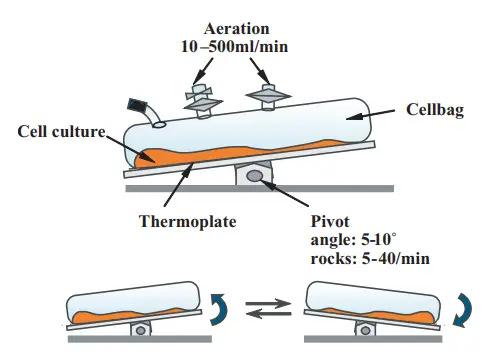
Types of Wave Bioreactor
Wave bioreactors mix and oxygenate cell cultures using mechanical waves. Various wave bioreactors create waves using different mechanisms:
- Magnetic Wave Bioreactors (MWBR): Magnetic fields produce mechanical waves in the culture media, allowing gentle mixing and mass transfer.
- Acoustic Wave Bioreactors (AWBR): Sound waves move the culture media, improving mixing and oxygenation.
- Pulsatile Wave Bioreactors (PWBR): Cyclic pressure fluctuations create mechanical waves that improve nutrient distribution and gas exchange.
- Hydrodynamic Wave Bioreactors (HWBR): HWBRs use fluid dynamics such regulated flow or pressure fluctuations to create mechanical waves that mix the culture media.
- Hybrid Wave Bioreactors: Using two or more of the above methods, hybrid wave bioreactors maximize mixing and mass transfer for specific applications.
Parts of Wave Bioreactor
Wave bioreactors mix and oxygenate culture media by rocking. Its main components are:
- Disposable Cell Culture Bag (Cellbag): A pre-sterilized, single-use bag with growth media and cells. Multilayer films provide mechanical strength and decrease contaminants.
- Rocking Platform (Rocker): An electric basis that controls Cellbag rocking. This action enhances culture mixing and aeration.
- Aeration System: The aeration system supplies oxygen and carbon dioxide to the culture. Often coupled with the Cellbag, it regulates dissolved gas.
- Temperature Control System: Includes rocking platform heaters to maintain culture temperature.
- Control Unit: Manages rocking speed, angle, temperature, pH, and dissolved oxygen. For accurate control and data logging, advanced systems require software interfaces.
- Sampling Port: Extracts culture samples without interrupting the sterile environment for frequent monitoring and analysis.
- Sterilization System: The Sterilization System cleans all parts before use. Although the Cellbag is disposable, some reusable elements may need sterilization.
Operating Procedure of Wave Bioreactor
The operating procedure of a wave bioreactor typically includes the following steps:
- Connect all required tubes for media, aeration, and sample by securely fastening the pre-sterilized disposable Cellbag to the rocking platform.
- Before beginning the culture, sterilize any reusable components and verify that the disposed of parts satisfy sterility criteria to reduce contamination hazards.
- Prepare the culture medium in line with the particular needs of the cell line so that the volume in the Cellbag follows the advised limitations of the system.
- Using aseptic methods to keep the bioreactor sterile during cell transfer, inoculate it with the intended cell suspension.
- Starting the rocking action, activate the platform at a designated frequency and angle to create wave-like motions mixing the culture and encouraging homogeneous oxygen distribution.
- By use of integrated sensors and control systems, continuously monitor important factors including temperature, pH, and dissolved oxygen, therefore modifying settings to preserve ideal conditions for development.
- To evaluate cell viability, density, and product yield without upsetting the culture, periodically remove samples through the designated sampling port under aseptic conditions.
- Harvest the cells or recombinant products following accepted downstream processing techniques after the culture achieves the target density or product accumulation.
- To be ready for next runs, finally dismantle the system by carefully throwing away the Cellbag and sterilizing any reusable parts in line with manufacturer instructions.
Applications of Wave Bioreactor
- Wave bioreactors are used to grow mammalian cells for biopharmaceuticals such recombinant proteins, monoclonal antibodies, and vaccinations.
- Their disposable cellbags reduce contamination and cleaning, making them perfect for GMP-compliant vaccine production and fast turnaround.
- A regulated and consistent culture environment for inoculum expansion and process optimization allows smooth scale-up from modest laboratory research to big commercial output.
- Growing primary cells, stem cells, and regenerative medicine cells requires moderate rocking to avoid shear stress on sensitive cells.
- Wave bioreactors maximize viral vector generation in gene therapy by guaranteeing uniform oxygen transport and exact growth conditions.
- For complicated protein and vaccine production, insect cell cultures use baculovirus expression systems.
- Since controlled wave-induced mixing permits exact parameter modifications and real-time monitoring, these devices help R&D labs optimize processes.
- High biomass yields for biofuel and nutraceutical development are possible with algae culture and improved oxygenation and mass transfer.
- Wave bioreactors’ modularity allows connection with modern control and data collecting systems for process validation and quality assurance.
Advantages of Wave Bioreactor
- Gentle wave movements in wave bioreactors improve oxygen transport and nutrition mixing while maintaining a consistent cell growth environment.
- Cleaning and sterilizing between runs is unnecessary with the disposable cellbag design, minimizing downtime and contamination hazards.
- Compared to stirred systems, their rocking action reduces shear stress, protecting delicate cell lines.
- Real-time monitoring and exact adjustment of pH, temperature, and dissolved oxygen via integrated control systems ensures ideal culture conditions.
- Scalability allows these systems to move from small-scale research to large-scale commercial production without losing process consistency.
- Wave bioreactors are ideal for high-quality biopharmaceutical production because their closed, aseptic design facilitates GMP compliance.
Limitations of Wave Bioreactor
- Many wave bioreactors are limited to 100 liters, making them unsuitable for large-scale industrial production.
- Rocking mixing reduces volumetric oxygen transfer rates, rendering them unsuitable for high-oxygen processes like microbial or yeast fermentations.
- They may suffer in viscous or heat-sensitive environments, limiting their adaptability for diverse cell types or sophisticated bioprocessing applications.
- Multiple moving parts increase the possibility of mechanical failure, which can disrupt culture and need costly repair or downtime.
- These systems require specialist training to optimize rocking speed, angle, and gas flow for each application.
- Disposable components decrease cleaning, however incorrect handling or sterilization of reusable parts may increase contamination hazards.
- Advanced control units and sensors can be expensive, making the technology unaffordable for certain labs and smaller manufacturing companies.
Precautions
When using a wave bioreactor, it is important to take the following precautions to ensure safe and effective operation:
- Always use gloves, safety goggles, and a lab coat to avoid exposure to harmful materials.
- Avoid very fluid, heat-sensitive, or particle-laden culture samples that may hinder mixing.
- To reduce contamination, sterilize all disposable parts and clean and sterilize reusable parts.
- Handle the bioreactor carefully since glass and stainless steel pieces can break during setup and operation.
- Follow the manufacturer’s guidelines and SOPs to avoid operational mistakes and system breakdowns.
- Maintain ideal cell growth conditions by monitoring temperature, pH, and dissolved oxygen with the integrated control system.
- Effective mixing without shear stress on sensitive cells requires careful rocking motion parameters like frequency and angle.
- To guarantee process continuity, create and maintain a strategy for equipment failure, power outages, and contamination.
- To ensure safe and effective wave bioreactor operation, train all staff on its usage, maintenance, and troubleshooting.
- After each usage, wash and sterilize to remove residual pollutants and avoid cross-contamination.
Reference
- Slivac, Igor & Srček, Višnja & Radošević, Kristina & Kmetič, Ivana & Kniewald, Zlatko. (2006). Aujeszky’s disease virus production in disposable bioreactor. Journal of biosciences. 31. 363-8. 10.1007/BF02704109.
- https://www.coleparmer.in/i/wave-bioreactor-system-2-110-220-vac-switchable/6120000
- https://www.selectscience.net/products/wave-bioreactor-systems/?prodID=86581#:~:text=and%2020%2F50-,The%20WAVE%20Bioreactor%20system%20is%20a%20cell%20culture%20device%20suitable,as%20the%20Cellbag%E2%84%A2%20bioreactor.
- Text Highlighting: Select any text in the post content to highlight it
- Text Annotation: Select text and add comments with annotations
- Comment Management: Edit or delete your own comments
- Highlight Management: Remove your own highlights
How to use: Simply select any text in the post content above, and you'll see annotation options. Login here or create an account to get started.