What is Single Use Bioreactor?
- A single use bioreactor is a bioreactor device whereby a disposable, pre-sterilized plastic bag derived from multilayer polymer films contacts the cell culture.
- It substitutes conventional glass or stainless steel vessels, therefore cutting the validation complexity and removing the requirement for cleaning and sterilizing procedures.
- Emerging in line with the larger trend toward disposable process solutions in biopharmaceutical production, the technology arrived in the late 1990s.
- Designed for upstream operations including medium and buffer preparation, cell cultivation, and harvesting in the manufacturing of biologics, vaccines, and cell treatments, single use bioreactors are intended
- To guarantee efficient mixing and oxygen transmission while preserving a sterile environment, they combine agitation techniques—either by rocking (wave bioreactor systems) or by integrated stirring mechanisms.
- Reduced turn-around times for changeover between batches, lower capital and operational expenses, less water, energy, and cleaning reagent use—all of which help to diminish risk of cross-contamination.
- Though present technology usually limits sizes to about 2000 liters, their design allows fast scalability from lab-scale to production-scale.
- Recent advances concentrate on combining modern, non-invasive sensors and automation for real-time process monitoring and control, hence improving process robustness and data logging.
- Particularly helpful for pre-commercial manufacturing and clinical trials, the general effect is a more versatile and efficient bioprocessing platform supporting agile manufacturing.
Working Principle of Single Use Bioreactor
- Operating as a closed, disposable system, the single use bioreactor uses a pre-sterilized plastic bag consisting of multilayer polymer films meant for cell interaction.
- Culture media and cells are added once the bag is set into a reusable support frame, therefore producing a sterile environment for cell development.
- Either an integrated stirring mechanism—often connected mechanically or magnetically—or a rocking (wave) motion that encourages mixing and effective oxygen transfer achieves agitation.
- Designed with layers for mechanical support, gas barrier qualities, and biocompatibility, the disposable bag reduces shear stress on delicate cells and helps to distribute nutrients properly.
- Embedded during manufacture, integrated non-invasive sensors (e.g., for pH, dissolved oxygen, temperature) allow real-time monitoring and control of the cultural environment without sacrificing sterility.
- The technology is meant to cut operational complexity and downtime by doing away with the necessity for sterilizing and cleaning between batches.
- Only the throwaway bag and related single-use components are thrown away following a manufacturing run; the support structure and control systems are kept for further usage.
Parts of Single Use Bioreactor
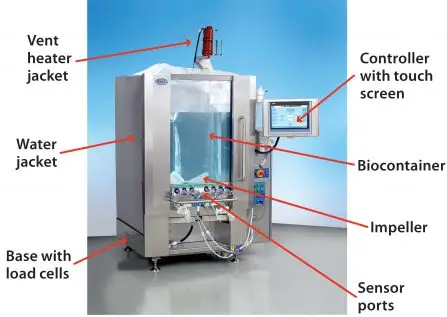
Comprising numerous essential components meant to enable effective and sterile biological operations, a single-use bioreactor (SUB)
- Disposable Bioreactor Bag – Usually composed of layered plastic films, the central component—the disposable bioreactor bag—is the cultural vessel. For mechanical stability, these films sometimes feature layers of polyethylene terephthalate (PET) or low-density polyethylene (LDPE), polyvinyl alcohol (PVA) or polyvinyl chloride (PVC) as gas barriers, and an inner contact layer of PVA or polypropylene (PP) to guarantee biocompatibility.
- Mixing System – Essential for preserving uniformity in the cultural media, SUBs use several agitation techniques. While some use a rocking motion to accomplish mixing without internal mechanical components, others use integrated mechanical stirrers connected either mechanically or magnetically.
- Aeration and Oxygenation System – These methods supply oxygen into the culture medium to enable cellular respiration. Gas sources (such as compressed air or oxygen tanks), gas distribution systems like spargers or diffusers to distribute gas uniformly, and flow controllers to control gas intake could all be components.
- Temperature Control System – Maintaining ideal temperatures is absolutely essential for cell survival and production. Along with inside temperature sensors, external heating or cooling systems—such as heating jackets or temperature-regulated water baths—are utilized to monitor and modify the cultural surroundings.
- pH Control System – pH sensors and controllers help SUBs to guarantee that the culture medium stays within the intended pH range. Crucially for cellular operations, these systems can inject bases or acids as needed to preserve ideal pH levels.
- Sterilization Port – Some SUBs include sterilizing ports that let operators add sterilizing agents, including hydrogen peroxide or ethylene oxide, so guaranteeing the sterility of the bioreactor before use.
- Control System – An integrated control system looks over and controls several variables, including temperature, pH, dissolved oxygen, and agitation speed. This system guarantees appropriate conditions for microbial development and metabolism by means of sensors and controllers, therefore preserving the bioreactor.
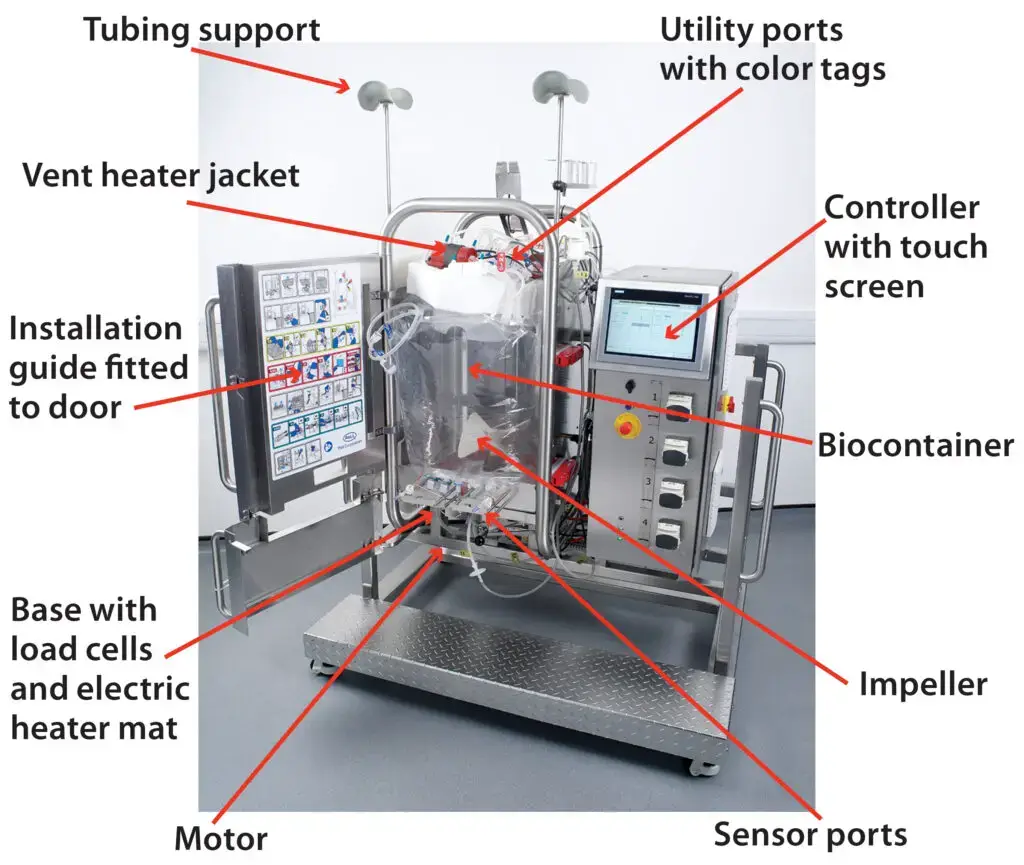
Types of Single Use Bioreactor
Offering disposable, pre-sterilized systems that cut turn-around times and eliminate the need for cleaning, single-use bioreactors (SUBs) have transformed bioprocessing. Mostly, these bioreactors are classified according to their mixing systems:
- Stirred Single-Use Bioreactors – Using integrated impellers inside the disposable bag, stirred single-use bioreactors replicate classic stirred-tank layouts. Whether mechanically or magnetically, the impellers are coupled to external drives to provide effective mixing and oxygen flow.
- Rocking Motion (Wave) Single-Use Bioreactors – Using a rocking platform, these single-use bioreactors mix the culture medium by the produced wave motion, so removing the need for internal mechanical agitators. Often used in seed-train applications, this design is especially fit for shear-sensitive environments.
- Airlift Single-Use Bioreactors – These single-use bioreactors mix the culture medium using the circulation of air or gas, therefore forming a loop that encourages mild mixing and oxygenation free from mechanical action.
- Bubble Column Single-Use Bioreactors – In bubble column single-use bioreactors, air or gas is supplied at the column’s base and the rising bubbles help to mix and oxygenate the growth media.
- Fluidized Bed Single-Use Bioreactors – These bioreactors effectively mix and mass transfer by supporting immobilized cells or enzymes from a fluidized bed of particles.
- Packed Bed Single-Use Bioreactors – Featuring a packed bed of support materials, packed bed single-use bioreactors allow immobilization of cells or enzymes, hence enabling constant processing and high output yields.
Operating Procedure of Single Use Bioreactor
- Start by making sure the disposable bioreactor bag, tubing, connectors, and integrated sensors—among other system components—are whole and sterile.
- Following manufacturer instructions, place the pre-sterilized disposable bag into the reusable support frame and tighten all connections.
- Verify that the temperature control, pH, and dissolved oxygen sensors are tuned and ready for use by connecting the bioreactor to the control system and power supply.
- Using the corresponding inlet port, introduce the culture medium into the bag such that no air bubbles become caught in the system.
- Use aseptic methods to inoculate the bioreactor with the suitable cell culture or microbial inoculum, hence preserving sterility.
- Choose the intended mixing mode—either mechanical stirring or rocking motion—to guarantee homogeneity in the culture media and sufficient oxygen transfer, so starting the agitation process.
- Connect the gas supply—air or oxygen—to the system to start the aeration process; change the gas flow rate to preserve ideal dissolved oxygen levels as shown by onboard sensors.
- Using the integrated control system, constantly track important parameters (temperature, pH, dissolved oxygen, and agitation speed) and make real-time changes as needed to keep ideal conditions in culture.
- Periodically sample the culture aseptically during the procedure to evaluate cell viability, growth, and product expression, thereby guaranteeing that the process is moving within specified parameters.
- After the production run ends, carefully harvest the cultural product via the assigned outlet using accepted procedures to prevent product loss or contamination.
- While keeping the reusable support frame and control system for next batches, dispose of the single-use components—e.g., the disposable bag and tubing—in conformity with environmental and legal recommendations.
Applications of Single Use Bioreactor
- By creating a sterile, disposable environment that reduces cross-contamination hazards, they are used in upstream processing for the manufacture of biologics such monoclonal antibodies, recombinant proteins, and vaccines.
- Perfect for preclinical research and clinical manufacturing, they enable fast cell culture development from laboratory size to pilot and commercial production.
- By removing cleaning validation processes and thereby lowering downtime, they promote flexible, multi-product manufacturing techniques in contract development and manufacturing companies.
- Process development and optimization studies make use of them so that simultaneous experimentation with reduced capital expenditure and faster turnaround times may take place.
- They are used in the manufacturing of cell treatments and regenerative medicine products, where cell viability and functionality depend on rigorous sterility and careful handling.
- They fit perfectly into whole single-use process systems covering medium preparation, cell harvesting, and downstream recovery operations, therefore optimizing the whole bioprocessing process.
- Because they can swiftly build up manufacturing lines and adjust to changing product needs, they are crucial in fast-response situations as the creation of a pandemic vaccination.
Advantages of Single Use Bioreactor
- Between batches, single use bioreactors eliminate the requirement for sterilization and cleaning, therefore lowering turn-around times and danger of contamination during process changeover.
- Their disposable character reduces equipment complexity, energy and water usage, and the cost of cleaning chemicals, therefore lowering both capital and running expenses.
- From laboratory research to pilot and clinical production, they provide great scalability and flexibility so producers may rapidly move between several products or production levels.
- Pre-sterilized, single use components help to lower the danger of cross-contamination, a major benefit for clinical uses and multi-product facilities.
- Real-time monitoring of important parameters (e.g., pH, temperature, dissolved oxygen) made possible by integrated non-invasive sensors and control systems guarantees consistent process control and enhanced product quality by means of which process control is assured.
- Single use systems’ modular architecture allows quick facility setup and adaption, therefore supporting agile production techniques and lowering the time-to–market for new biologics.
- Although they use throwaway materials, lifespan analyses may demonstrate that, in terms of water, energy, and chemicals, the lower overall environmental impact of the reduced resource consumption throughout operation might result from classic stainless steel systems over other systems.
- Early-stage clinical production and process development, where speed and flexibility are crucial, finds them particularly appealing for their streamlined design and low maintenance needs.
Limitations of Single Use Bioreactor
- Gentle agitation settings—necessary to minimize shear damage—may limit oxygen transfer capacity, therefore restricting cell density and general productivity.
- The physical characteristics of the disposable bag limit scale-up; increased internal pressure could cause material failure or leakage as capacity rises.
- Using plastic materials begs questions regarding extractables and leachables that can impair product purity and influence cell viability.
- Variability in disposable components batch-to- batch could provide difficulties for consistent process performance and repeatability.
- Although energy and water use may be less, end-of- life disposal and environmental effect remain issues for single-use systems since they produce notable amounts of plastic waste.
- Integration of fixed, pre-installed sensors reduces flexibility for calibration or replacement, therefore influencing the accuracy of real-time monitoring.
- Although first capital expenses are less, the regular cost of disposable components might mount over time and could affect long-term process economics.
Precautions
- Before use, check the integrity of every throwaway component to make sure the connectors, tubing, and bioreactor bag indicate no sterility compromise or damage.
- During assembly, inoculation, sampling, and harvest, follow aseptic methods exactly to reduce contamination risk.
- Since these built-in components cannot be readily replaced or recalibrated once installed, make sure integrated sensors—for pH, temperature, dissolved oxygen, etc.—are correctly calibrated and operating.
- Closely control agitation and aeration settings to preserve ideal mixing and oxygen transmission and avoid too strong shear stress that can damage delicate cells.
- To stop leaks or rupture in high-density or high-volume cultures, note the operational limits of the disposable bag, especially with relation to internal pressure and volume.
- Considering possible extractables and leachables that can compromise product purity, assess if reagents and culture media fit the plastic materials of the bioreactor.
- Track performance variability by keeping thorough documentation and batch records, therefore making sure any variations in disposable component quality are found and corrected.
- Following manufacturer and legal recommendations for the correct disposal of discarded components will help to lower environmental effect and guarantee compliance with safety criteria.
- Review process validation and quality control data periodically to evaluate single-use system consistency and repeatability under various production settings.
Reference
- https://www.sartorius.com/en/products/fermentation-bioreactors/single-use-bioreactors#:~:text=Single%2Duse%20bioreactors%20are%20used,and%20disposed%20of%20after%20use.
- https://bionet.com/technology/single-use-bioreactors/
- https://www.cytivalifesciences.com/en/us/solutions/bioprocessing/products-and-solutions/upstream-bioprocessing/single-use-bioreactors
- https://www.pharmtech.com/view/pros-and-cons-single-use-bioreactors
- https://boydbiomedical.com/articles/the-rise-of-single-use-bioreactors-why-make-the-switch
- https://bioprocessintl.com/upstream-processing/upstream-single-use-technologies/superior-scalability-single-use-bioreactors/
- https://bioprocessintl.com/2016/design-performance-single-use-stirred-tank-bioreactors/
- https://www.thermofisher.com/in/en/home/life-science/bioproduction/single-use-bioprocessing/single-use-equipment/single-use-bioreactors/open-architecture-single-use-bioreactors.html
- https://web.wpi.edu/Images/CMS/BEI/parrishgalliher.pdf
- https://pharmaceuticalmanufacturer.media/pharmaceutical-industry-insights/biopharma-news/single-use-vs-stainless-steel-bioreactors-which-to-choose/
- http://technologyinscience.blogspot.com/2013/07/single-use-bioreactor-types-advantages.html#.Y8JVYXZBy5c
- Text Highlighting: Select any text in the post content to highlight it
- Text Annotation: Select text and add comments with annotations
- Comment Management: Edit or delete your own comments
- Highlight Management: Remove your own highlights
How to use: Simply select any text in the post content above, and you'll see annotation options. Login here or create an account to get started.