What is Incinerator?
- An incinerator is a specialized furnace designed for the purpose of burning potentially dangerous materials in a controlled combustion chamber. It involves the process of incineration, which refers to the high-temperature burning of waste materials to eliminate pollutants.
- Incineration is commonly employed in situations where there is a large accumulation of waste and when the treatment of bulky and heterogeneous waste is necessary. It can effectively handle various hazardous pollutants, including soil, sludge, liquids, and gases. During incineration, the organic portion of the waste is burned, producing heat, while the inorganic content generates ash. Additionally, combustion gases are also produced as byproducts of the process.
- The primary objective of incineration is to destroy and neutralize dangerous substances present in the waste. This process can effectively eliminate pollutants such as solvents, PCBs (polychlorinated biphenyls), and pesticides. However, it should be noted that certain metals, including lead and chromium, are not eliminated through incineration.
- Incinerators are commonly used for the safe disposal of solid, liquid, and gaseous waste generated from various manufacturing processes. In addition to waste disposal, incinerators can also be utilized to generate electricity or produce heat by utilizing the energy released during the incineration process. This is often achieved through the use of auxiliary equipment like steam boilers.
- To mitigate the potential negative impacts on the environment, modern incinerators are equipped with air pollution control technologies. These technologies help minimize the release of harmful emissions into the atmosphere, ensuring that the incineration process is conducted in an environmentally responsible manner.
- In summary, an incinerator is a specialized furnace used for the controlled burning of potentially dangerous materials. Through the process of incineration, it effectively treats and neutralizes hazardous pollutants in waste while generating heat, ash, and combustion gases as byproducts. Incinerators play a crucial role in the safe disposal of waste materials, and advancements in technology have allowed for greater environmental protection during the incineration process.
Definition of Incinerator
An incinerator is a specialized furnace designed for burning potentially dangerous materials in a controlled manner, typically at high temperatures, to eliminate pollutants and safely dispose of waste.
Working principle of Incinerator
The principle of an incinerator is based on a two-stage combustion process, involving a primary combustion chamber and a secondary combustion chamber.
In the design of an incinerator, a primary combustion chamber is specifically intended for the burning of solid waste or sludge oil. This chamber is equipped with a primary burner, which initially receives diesel oil for ignition. Once ignited, the primary burner is then supplied with sludge oil, either manually or automatically, until it ignites. To facilitate effective combustion, the sludge burner receives atomizing air. The amount of sludge entering the conversion chamber can be controlled through a pressure-regulating valve on the sludge return line.
When the heat from the primary burner is applied, solid waste will dry out and begin to burn, and the sludge oil may also catch fire. The gases produced during the primary combustion process proceed to the secondary combustion chamber. This secondary chamber is responsible for burning out any unburned exhaust gases to further minimize pollutants.
To separate the primary and secondary combustion chambers, a wall of ceramic heavy-duty refractory liners is installed. This division helps contain and control the combustion process within each chamber.
In cases where solid waste or garbage is being incinerated, it is fed into the incinerator through a feeding door. It is important to note that the primary burner cannot be ignited if this door is open. However, the rest of the combustion process continues as usual.
By employing the principle of a two-stage combustion process, with separate primary and secondary chambers, an incinerator ensures efficient and controlled burning of waste materials while minimizing the release of pollutants into the environment.
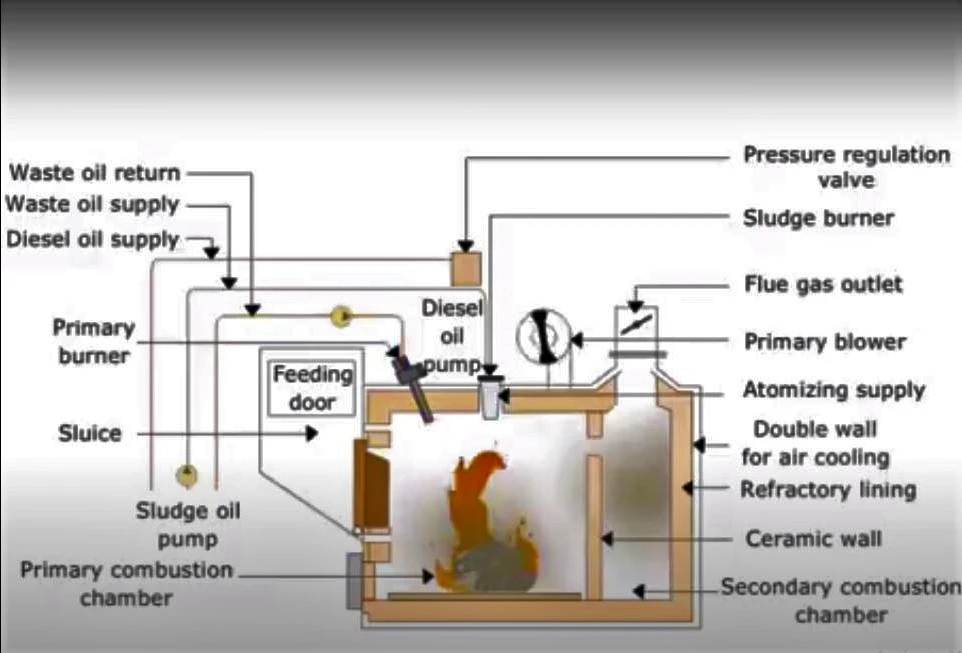
Operating procedure of Incinerator
The operating procedure of an incinerator involves several key steps to ensure the safe and efficient combustion of waste materials. While specific procedures may vary depending on the type and model of the incinerator, the following general steps can be considered:
- Preparing the incinerator: Ensure that the incinerator is in proper working condition, with all necessary maintenance and safety checks performed. Verify that the primary and secondary combustion chambers are clean and ready for operation.
- Preparing the fuel: If required, ensure that the primary burner is supplied with the initial ignition fuel, such as diesel oil. This fuel is used to ignite the primary burner and initiate the combustion process.
- Starting the incineration process: Ignite the primary burner using the initial ignition fuel. Once the primary burner is ignited, switch to the sludge oil as the primary fuel source for the combustion process. Monitor the ignition process to ensure that the sludge oil ignites properly.
- Adjusting combustion parameters: To facilitate effective combustion, provide atomizing air to the sludge burner. This helps optimize the burning of sludge oil and ensures efficient incineration.
- Controlling sludge input: Utilize the pressure-regulating valve on the sludge return line to control the amount of sludge entering the conversion space. Adjust the valve as needed to maintain the desired sludge input for optimal combustion.
- Combustion in primary chamber: The heat generated by the primary burner will cause the solid waste to dry out and begin burning. Simultaneously, the sludge oil will ignite and contribute to the combustion process. The primary combustion chamber’s design, including its transmission area, aids in the drying and burning of solid waste.
- Secondary combustion chamber: The gases produced in the primary combustion chamber proceed to the secondary combustion chamber. The unburned exhaust fumes are burned off in this chamber to ensure complete combustion and minimize pollutants. The primary and secondary combustion chambers are separated by a wall of ceramic heavy-duty refractory liners.
- Waste feeding: In the case of solid waste or garbage, feed the waste into the incinerator through the feeding door. It is essential to ensure that the feeding door is closed during the combustion process to prevent interference with the primary burner. However, the rest of the combustion process continues as usual.
- Monitoring and safety checks: Continuously monitor the combustion process, ensuring that the incinerator is functioning correctly and safely. Regularly check for any abnormalities, leaks, or malfunctions that may affect the combustion or safety of the incinerator.
- Shutting down the incinerator: Once the incineration process is complete or when the waste feeding is finished, follow the appropriate shutdown procedure. This may involve extinguishing the primary burner, allowing the system to cool down, and performing necessary cleaning and maintenance tasks.
It is important to refer to the specific operating manual provided by the manufacturer of the incinerator and follow their guidelines and instructions for safe and efficient operation.
Parts of Incinerator
An incinerator consists of various parts that work together to facilitate the combustion and disposal of waste materials. The following are the common parts of an incinerator:
- Primary Chamber: This is where the waste is initially loaded and burned. The primary chamber allows the waste to vaporize, and the low air-to-fuel ratio helps in drying and carbon combustion.
- Secondary Chamber: The waste-derived volatile substances from the primary chamber are transferred to the secondary chamber. Here, additional air is injected to ensure complete combustion of the volatile gases. The higher temperatures in the secondary chamber promote the oxidation of gaseous products.
- Flue Stack: Also known as the chimney, the flue stack is responsible for releasing the exhaust gases into the atmosphere. The stack height requirements vary depending on local regulations and environmental considerations.
- Control Panel and Thermocouples: These components regulate and monitor the incinerator’s operation. They ensure that the chambers reach the required temperature before loading waste for incineration.
- Burners: Burners are used to heat up the incinerator, and they are often turned off during the combustion process. Modern incinerators may include low NOx or variable gas flow burners.
- Fuel Tanks: Fuel tanks store the fuel, which can be solid waste, used by the burners during the incineration process.
- Combustion Chamber (Primary Chamber): The primary chamber is where the waste is loaded and ignited. It operates at high temperatures, reducing the waste to ash and gases.
- Pollution Control Equipment: This includes filters, scrubbers, and other devices that remove pollutants from the exhaust gases before they are released into the atmosphere. These control measures ensure compliance with environmental regulations.
- Ash Handling: Ash handling equipment is responsible for collecting and disposing of the ash produced during the incineration process.
- Electrical Equipment: Generators, control systems, and other electrical components are used to operate and control the incinerator.
- Cooling System: The cooling system helps reduce the temperature of the exhaust gases before they are released into the atmosphere. This ensures that the gases are safe to be discharged.
- Stack: The stack, also known as the chimney or flue stack, is the component that exhausts the gases into the atmosphere.
These are some of the essential parts commonly found in an incinerator. The specific design and components may vary depending on the type and model of the incinerator and the regulatory requirements of the operating location.
The Incineration Process
- Combustion: Continuous waste is fed into the furnace by an overhead crane for combustion. To prevent the development of dioxins and carbon monoxide, the waste is burned in a specifically built furnace at a high temperature of > 850oC for more than 2 seconds with a sufficient supply of air to assure complete combustion of the waste.
- Boiler/steam turbine: The boiler uses the heat from the combustion to generate steam. The steam subsequently drives the turbine, which is attached to the generator of energy. The created extra heat can also be used for other reasons, such as heating a swimming pool.
- Exhaust gas cleaning: The boiler’s exhaust gas is normally cleaned by the following advanced pollution control systems to ensure compliance with demanding environmental regulations.
- Dry or Wet Scrubbers: To spray lime powder or fine atomized slurry into the hot exhaust gas to neutralise and remove the acidic pollutants (sulphur oxides, hydrogen chloride).
- Activated Carbon Injection: To absorb and eliminate heavy metal and organic contaminants (such as dioxins) from exhaust gas.
- Bag house filter: To filter and remove dust and small particles using a bag house filter.
- Selective Non-Catalytic Reduction: To eliminate a nitrogen oxide (a pollutant that contributes to urban smog) by reacting it with ammonia or urea.
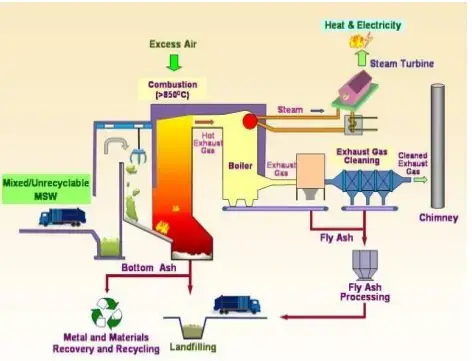
Input materials
Multiple factors influence the quality and amount of MSWI inputs and outputs:
- Households and industrial or commercial establishments are waste producers.
- Waste prevention (theoretically) influences both residential and industrial waste production.
- Separate collection has a substantial effect on the quantity and quality of incinerable garbage. For instance, the collection of small electrical equipment separately could lower Cu levels in MSWI bottom ash by up to 80%. By separating recyclables and biodegradable waste at the source, the amount of waste requiring treatment is drastically decreased.
- Residues from waste processing technologies (e.g., sorting of plastics after separate collection) and other items may also be included in the MSWI input.
MSWI residue
Different solid and liquid residual products as well as gaseous effluents are produced by the incineration process. On a moist basis, approximately one-fourth of the waste material remains as solids. The volume of residues equals one-tenth of the initial amount of garbage. The typical leftovers of MSWI combustion by grate are:
- A quenching/cooling tank collects bottom ash, which consists mostly of coarse noncombustible debris and unburned organic matter, near the combustion chamber’s output.
- Grate siftings, which consist of relatively fine materials flowing through the grate and accumulating at the bottom of the combustion chamber. Most of the time, it is impossible to separate grate siftings and bottom ash, as they are typically mixed together. Typically, bottom ash and grate siftings account for 20 to 30 percent by mass of the original wet waste.
- Boiler and economizer ash, which is the coarse fraction of the particles transported by the exhaust gases from the combustion chamber and collected at the heat recovery section. This stream may account for up to 10 percent of the original waste’s mass on a dry basis.
- Before further treatment of the gaseous effluents, fly ash, the fine particulate matter remaining in the flue gases after the heat recovery units, is removed. On a wet basis, the quantity of fly ash produced by an MSW incinerator is between 1 and 3 percent of the waste input mass.
- Air pollution control (APC) residues, comprising particle matter caught following reagent injection in acid gas treatment units prior to effluent gas release into the atmosphere. This residue may be solid, liquid, or sludge, depending on whether dry, semi-dry, or wet procedures for air pollution management are utilised. On a wet basis, APC leftovers are typically between 2% and 5% of the original waste.
Types of Incinerator
There are various categories of commercial combustion technologies:
- Rotary Kiln Incinerator
- Fluidized Bed Incinerator
- Moving Grate Incinerator
- Multiple Hearth Incinerator
- Liquid injection Incinerator
- Catalytic combustion chamber
- Waste gas flare incinerator
- Fixed Grate Incinerator
1. Rotary Kiln Incinerator
A rotary kiln incinerator is a thermal treatment system designed for the combustion and disposal of various waste types. The key features and characteristics of a rotary kiln incinerator are as follows:
- Thermal Treatment Chambers: The rotary kiln incinerator consists of two thermal treatment chambers. The primary chamber is slightly slanted and where waste is fed along with hot exhaust air containing oxygen. In this chamber, the waste is rotated and thermally decomposed through heat radiation from the secondary chamber. The secondary chamber, located at the back of the kiln, serves as a recombustion chamber. It ensures the complete burning of the decomposition air and the remaining waste with the supply of secondary air.
- Rotating Combustion Chamber: The incinerator is built with a rotating combustion chamber that continuously circulates the waste. The rotation helps in facilitating the vaporization of waste, making it easier to burn. The inclination angle and rotational rate of the kiln can be adjusted to manage the waste throughput rate.
- High Burnout Rates: Rotary kiln incinerators offer higher solids burnout rates and greater particulate entrapment in the flue gas compared to other incinerator designs. The turbulent motion of waste in the primary chamber contributes to these higher rates. As a result, gas cleaning accessories are often incorporated to ensure efficient cleaning of the flue gas.
- Advantages: Rotary kiln incinerators have several advantages. They produce less nitrogen oxide (NOx) emissions compared to other incinerator designs. The design of the incinerator allows for effective heat elimination of hazardous compounds present in the waste, ensuring efficient and safe combustion.
- Waste Types: Rotary kiln incinerators are suitable for treating various waste types, including pharmaceutical waste, hazardous waste, and medical waste. Examples of medical waste that can be treated in a rotary kiln incinerator include sharps, infectious waste, surgical trash, clinical waste, and laboratory waste.
Overall, rotary kiln incinerators provide a reliable and efficient method for the thermal treatment and disposal of different waste streams. Their design features and capabilities make them suitable for handling a wide range of waste types, contributing to effective waste management and environmental protection.
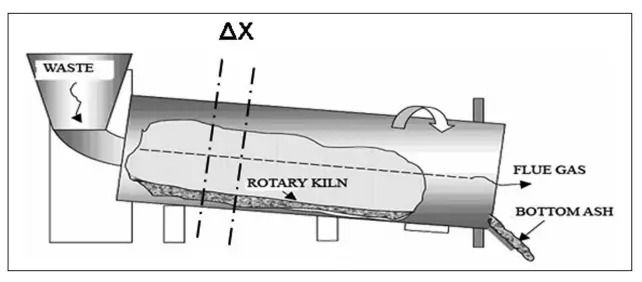
2. Fluidized Bed Incinerator
A fluidized bed incinerator is a type of incineration system that utilizes the principle of fluidization to efficiently burn waste materials. The key features and principles of a fluidized bed incinerator are as follows:
- Principle of Fluidization: Fluidization is the process of passing a fluid (typically air) through a bed of granular material to transform it into a fluid-like state. In the case of a fluidized bed incinerator, the reactor consists of a vertical steel vessel lined with refractory material and filled with a bed of granular material, such as limestone, silica sand, or ceramic material.
- Fluidization Process: Air is injected into the bed through multiple nozzles located at the bottom of the incinerator. The injected air creates a fluidized state within the bed, causing the bed material to exhibit fluid-like behavior. This results in a vigorous agitation of the bed material, facilitating the combustion of waste materials. The waste materials burn in close contact with the bed material and combustion air.
- Efficient Combustion: The fluidized bed incinerator achieves high thermal efficiency, often up to 90%, due to the relatively low excess air level made possible by the fluidization process. The close contact between the waste materials, bed material, and combustion air promotes efficient and thorough combustion.
- Waste Types: Fluidized bed incinerators are commonly used for the incineration of homogenous waste types, including sewage sludge and industrial waste. They can also handle liquid waste effectively. These incinerators are designed to handle specific waste streams that can be effectively combusted in a fluidized bed environment.
Fluidized bed incinerators offer several advantages, including efficient combustion, high thermal efficiency, and the ability to handle specific waste types. The violent agitation of the bed material in a fluidized state ensures effective mixing and combustion, while the controlled injection of air allows for optimized combustion conditions. These incinerators are widely used in industries and facilities that require the safe and efficient disposal of waste materials while minimizing environmental impact.
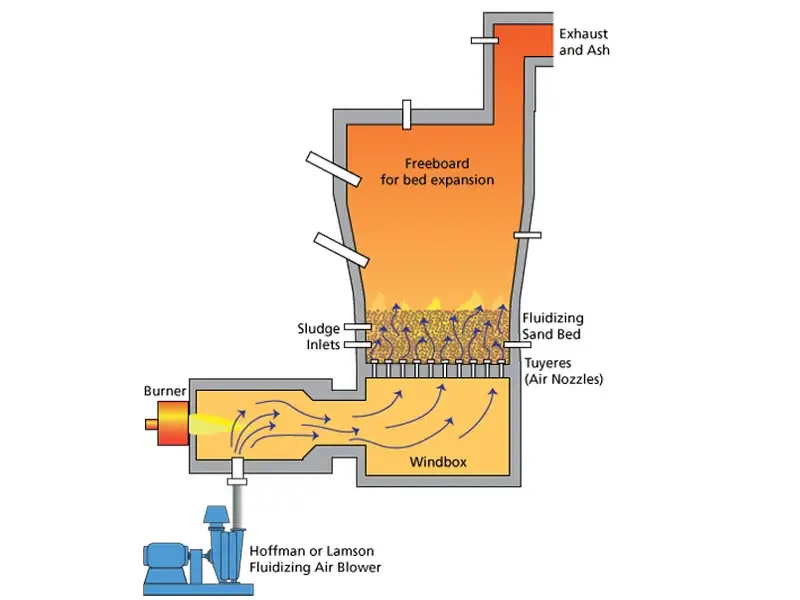
3. Moving Grate Incinerator
A moving grate incinerator is a type of incineration system that utilizes a moving grate to burn waste materials efficiently. The key features and principles of a moving grate incinerator are as follows:
- Grate Movement: In a moving grate incinerator, the waste is burned in layers on a grate that moves the waste through the furnace. The grate is designed to transport the waste gradually from one end of the furnace to the other. This movement allows for the controlled and sequential combustion of the waste.
- Drying and Combustion: As the waste moves along the grate, it is dried and preheated before reaching the combustion zone. The waste is then burned at a high temperature with the supply of air. The moving grate ensures that each layer of waste is exposed to the combustion zone, facilitating efficient and thorough combustion.
- Ash and Slag Removal: The non-combustible waste fractions, including ash, exit the grate through an ash chute as slag, also known as bottom ash. The bottom ash drops into a water trap and is cooled by coming into contact with cooling water. It then moves on to a conveyor system for further processing and disposal. Typically, a portion of the waste feed, around 10 to 25 percent by weight, is converted into slag.
- Advantages: Moving grate incinerators offer several advantages. Firstly, they utilize well-proven technology that has been widely used in waste-to-energy plants. They are capable of accepting a wide range of waste compositions and heat values, making them versatile for different waste streams. Additionally, moving grate incinerators can be produced in large units, allowing for efficient processing of substantial waste volumes.
- Drawbacks: One primary drawback of moving grate incinerators is the relatively high cost associated with their investment and maintenance. The complexity of the moving grate system and the need for regular maintenance can contribute to higher operating expenses compared to other incineration technologies.
Moving grate incinerators have been extensively used in waste management facilities worldwide. Their well-established technology, ability to handle diverse waste compositions, and scalability make them suitable for large-scale waste-to-energy applications. However, the costs involved should be carefully considered when evaluating the feasibility of implementing a moving grate incinerator.
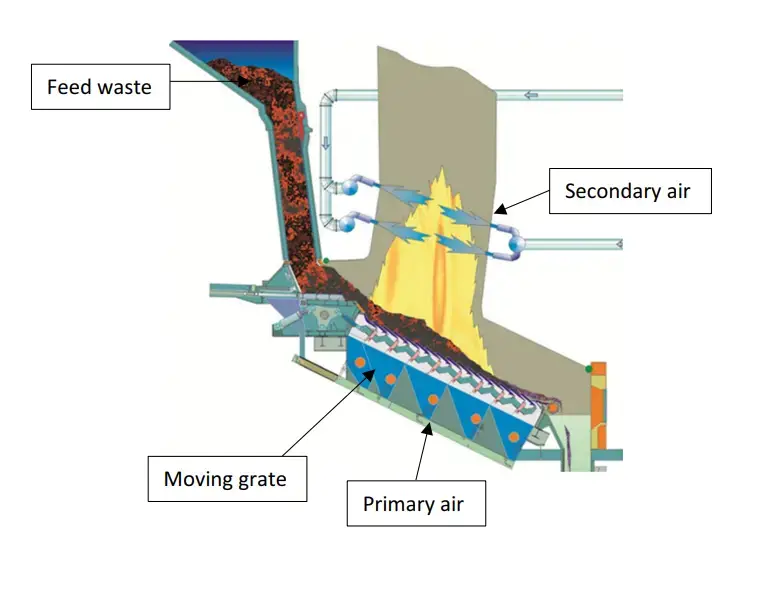
4. Multiple Hearth Incinerator
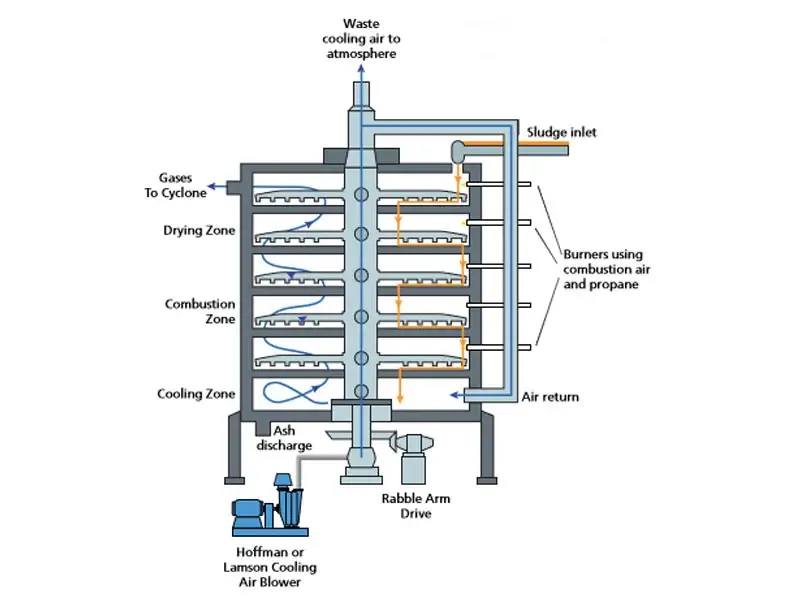
- The multiple hearth incinerator operates by feeding the waste material into the top of the incinerator. The waste then moves in a spiral pattern across each hearth, facilitated by a set of rabble arms attached to a vertical rotating shaft. These rabble arms agitate and distribute the waste evenly on each hearth, allowing for efficient combustion.
- As the waste progresses through each hearth, it undergoes the combustion process. The high temperatures within the incinerator, typically ranging from 1400 to 1800°F, ensure the thermal decomposition of the waste. The refractory-lined steel shell provides insulation and protection against the intense heat.
- After the waste has completed its residence time on a particular hearth, it drops through openings or chutes into the hearth below. This downward movement ensures a continuous flow of waste through the incinerator. The process repeats as the waste moves through each hearth, progressing toward the bottom of the incinerator.
- At the bottom hearth, the waste material is cooled, and the resulting ash, along with other non-combustible fractions, is discharged through an outlet. The ash handling equipment collects and manages the ash for proper disposal or further processing.
- Multiple hearth incinerators are commonly used for the treatment of various types of waste, including municipal solid waste, sludge, and other organic materials. The controlled movement of the waste through the multiple hearths allows for extended residence time, promoting more thorough combustion and reducing the presence of unburned materials.
- The advantages of multiple hearth incinerators include their ability to handle a wide range of waste compositions and heat values. The independent burners for each hearth enable precise control of the combustion process, resulting in efficient and effective waste treatment. However, it is important to note that multiple hearth incinerators can be relatively expensive to install and maintain due to their complex design and operation.
5. Liquid injection Incinerator
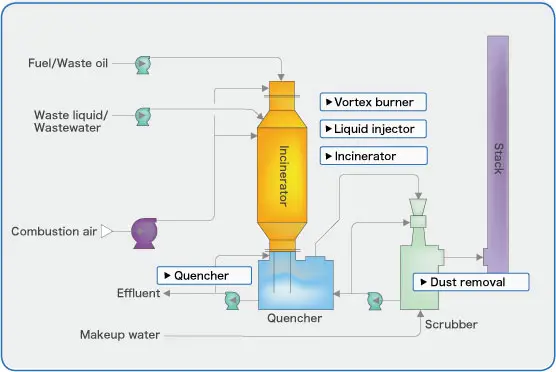
A liquid injection incinerator is a specialized device used for the efficient combustion of liquid waste. This incinerator operates by injecting liquid waste directly into the hot gases within the combustion chamber. The liquid waste is first atomized into fine droplets through the use of nozzles or atomization equipment. These small droplets allow for optimal mixing with air, facilitating rapid and complete combustion.
Operating at high temperatures typically ranging from 1200 to 3000°F, the injected liquid waste undergoes instant oxidation and conversion in the presence of heat and gases. This ensures the efficient destruction of organic combustible materials as well as non-combustible impurities in water. To be suitable for liquid injection incineration, the waste must exhibit liquid behavior with a viscosity of no more than 10,000 ssu (Saybolt Seconds Universal).
The main advantage of a liquid injection incinerator is its ability to effectively handle and combust liquid waste. The atomization of the liquid waste into a fine mist maximizes the surface area exposed to the flame, promoting thorough combustion and minimizing emissions. This incineration method is commonly employed for various types of liquid waste, including hazardous and industrial liquids.
The key components of a liquid injection incinerator include:
- Fuel storage: This is where the liquid waste is stored before it is injected into the combustion chamber for burning.
- Combustion chamber: This is the central chamber where the high-temperature combustion of the liquid waste takes place, reducing it to ash and gases.
- Atomization equipment: This equipment is responsible for breaking down the liquid waste into fine droplets to facilitate efficient combustion.
- Pollution control equipment: Filters, scrubbers, and other pollution control devices are utilized to remove pollutants from the exhaust gases before they are released into the atmosphere.
- Ash handling: Equipment is employed to collect and handle the ash generated during the incineration process.
- Electrical equipment: Generators, control systems, and other electrical components are utilized to operate and control the incinerator.
- Cooling system: This system is responsible for cooling the exhaust gases before they are discharged into the atmosphere to meet environmental regulations.
- Stack: The stack serves as the outlet through which the exhaust gases from the incinerator are released into the atmosphere.
- Control system: This includes the necessary controls and monitoring equipment to operate and regulate the incinerator’s processes effectively.
Liquid injection incinerators offer an efficient and reliable solution for the disposal of liquid waste, ensuring proper waste management and environmental protection.
6. Catalytic combustion chamber
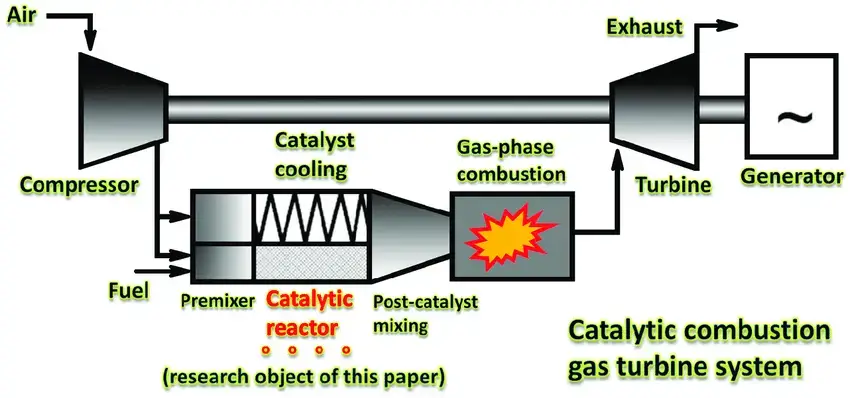
In the field of waste management and combustion, the catalytic combustion chamber has emerged as a significant advancement. Initially discovered by Engelhard Corp. in the 1970s, this process utilizes a catalyst to accelerate the desired oxidation reactions of fuel while minimizing the formation of undesirable byproducts, particularly nitrogen oxide (NOx) emissions. Catalytic combustion chambers are specifically designed for low organic concentration waste and play a crucial role in reducing air pollution and developing cost-effective waste management strategies.
Catalytic incinerators are primarily employed to eliminate gaseous pollutants, including volatile organic compounds (VOCs). VOCs are chemicals that readily transform into gases and contribute to air pollution. By utilizing a catalyst, catalytic incinerators enhance the rate of oxidation reactions, enabling the reduction of pollutants at lower temperatures compared to conventional incinerators. This not only improves energy efficiency but also aids in meeting stringent emission standards.
A catalytic combustion chamber consists of various essential components:
- Fuel storage: This is where the fuel, typically in the form of gas, is stored before undergoing combustion.
- Combustion chamber: The combustion chamber serves as the primary area where the fuel is burned in the presence of the catalyst. It provides the necessary conditions for efficient combustion.
- Catalyst: The catalyst, a substance with unique properties, facilitates and promotes the chemical reactions involved in the combustion process. It accelerates the oxidation of fuel and aids in reducing the formation of pollutants.
- Pollution control equipment: This includes filters, scrubbers, and other devices that effectively remove pollutants from the exhaust gases, ensuring compliance with environmental regulations and minimizing the release of harmful substances into the atmosphere.
- Ash handling: As combustion takes place, ash is generated as a byproduct. Proper ash handling equipment is necessary to collect and dispose of the ash safely and efficiently.
- Electrical equipment: Electrical components, such as generators and control systems, are crucial for operating and controlling the catalytic combustion chamber, ensuring its optimal performance.
- Cooling system: A cooling system is employed to reduce the temperature of the exhaust gases before they are released into the atmosphere. This helps prevent damage to the surrounding environment and maintains the safety of the overall system.
- Stack: The stack, also known as the chimney or exhaust pipe, provides a pathway for the discharge of the treated exhaust gases into the atmosphere.
- Control system: The control system encompasses the necessary equipment and technologies for operating, monitoring, and regulating the catalytic combustion chamber. It ensures the efficient functioning of the chamber and enables adjustments to be made as needed.
In summary, catalytic combustion chambers offer a highly efficient and environmentally friendly solution for waste management and combustion processes. By utilizing catalysts, these chambers promote complete combustion, reduce emissions, and enhance energy efficiency. Their applications span various industries, including industrial processes, commercial heating systems, vehicles, and power generation. As the demand for sustainable waste management strategies grows, catalytic combustion chambers play a vital role in minimizing environmental impact and advancing towards a cleaner future.
7. Waste gas flare incinerator
A waste-gas flare incinerator is an essential device used to burn off waste gases and liquids produced by various industrial activities. It finds applications in sectors such as oil and gas extraction, refineries, chemical plants, coal industry, and landfills. The purpose of a waste-gas flare incinerator is to combust undesirable or excess gases and liquids, preventing their release into the atmosphere.
Gas flaring, which is the process carried out by waste-gas flare incinerators, plays a significant role in reducing the environmental impact of industrial activities. It helps mitigate greenhouse gas emissions, which are a substantial contributor to climate change. By burning off the waste gases, the incinerator converts them into heat and other byproducts, ensuring that they do not contribute to air pollution or further degradation of the environment.
The main components of a waste-gas flare incinerator include:
- Fuel storage: This is where the waste gases and liquids are collected and stored before they are burned. It provides a controlled environment for efficient combustion.
- Combustion chamber: The combustion chamber is the central area where the waste gases and liquids are burned at high temperatures. It ensures complete combustion and the reduction of pollutants.
- Burner: The burner is responsible for igniting the waste gases and providing the necessary heat for the combustion process to occur.
- Pollution control equipment: Filters, scrubbers, and other pollution control devices are employed to remove pollutants and impurities from the exhaust gases before they are released into the atmosphere. This helps in minimizing the environmental impact.
- Ash handling: As the combustion process takes place, ash is generated as a byproduct. Adequate ash handling equipment is necessary to collect and dispose of the ash in a safe and environmentally friendly manner.
- Electrical equipment: Electrical components such as generators and control systems are essential for the operation and control of the waste-gas flare incinerator. They ensure the incinerator functions efficiently and can be monitored and adjusted as needed.
- Cooling system: A cooling system is employed to cool down the exhaust gases before they are released into the atmosphere. This prevents any potential damage to the surrounding environment and ensures safe operation of the incinerator.
- Stack: The stack, also known as the chimney or exhaust pipe, provides a pathway for the treated exhaust gases to be released into the atmosphere, effectively directing them away from the immediate surroundings.
- Control system: The control system includes various equipment and technologies used to operate, monitor, and regulate the waste-gas flare incinerator. It allows for the optimization of the incinerator’s performance and ensures compliance with environmental regulations.
The waste-gas flare incinerator is a crucial tool in industrial waste management, helping to control emissions, reduce pollution, and minimize the environmental footprint of various industrial processes. By efficiently burning off waste gases and liquids, it contributes to a cleaner and more sustainable approach to industrial activities.
8. Fixed Grate Incinerator
A fixed grate incinerator is a commonly used type of incinerator that is designed to efficiently burn solid waste. It employs a fixed grate or bed where the waste is placed and burned at high temperatures. The direct flame generated by the fuel and oxygen allows for the effective combustion of the waste materials.
One of the main advantages of a fixed grate incinerator is its ability to facilitate the complete burning of solid waste. The waste is continuously fed onto the fixed grate, ensuring a controlled and regulated combustion process. This controlled burning leads to reduced emissions and higher overall efficiency in waste disposal.
The key components of a fixed grate incinerator include:
- Fuel storage: This is where the fuel, typically in the form of solid waste, is stored before it is burned. It ensures a steady supply of fuel for the incineration process.
- Combustion chamber: The combustion chamber is the central area where the waste is burned at high temperatures. It provides the necessary environment for complete combustion and the reduction of waste to ash and gases.
- Grate: The fixed grate or bed is the platform where the waste is placed for burning. It provides stability and support to the waste during the combustion process.
- Pollution control equipment: Filters, scrubbers, and other pollution control devices are integrated into the system to remove pollutants from the exhaust gases before they are released into the atmosphere. This helps minimize the environmental impact of the incineration process.
- Ash handling: As the waste is burned, ash is produced as a byproduct. Adequate ash handling equipment is necessary to collect and dispose of the ash safely and efficiently.
- Electrical equipment: Electrical components such as generators and control systems are essential for the operation and control of the fixed grate incinerator. They ensure the incinerator functions properly and can be monitored and adjusted as needed.
- Cooling system: A cooling system is implemented to cool down the exhaust gases before they are released into the atmosphere. This helps prevent potential damage to the surrounding environment and ensures safe operation of the incinerator.
- Stack: The stack, also known as the chimney or exhaust pipe, serves as an outlet for the treated exhaust gases to be released into the atmosphere, directing them away from the immediate surroundings.
- Feeding system: The feeding system includes equipment and mechanisms used to continuously feed the waste onto the fixed grate. It ensures a steady supply of waste for the combustion process.
- Control system: The control system comprises various equipment and technologies used to operate, monitor, and regulate the fixed grate incinerator. It allows for efficient control of the incineration process and ensures compliance with environmental regulations.
Fixed grate incinerators are widely used for the disposal of various types of waste, including municipal solid waste, industrial waste, agricultural waste, and more. They provide a reliable and effective method for waste management, contributing to the reduction of waste volume and minimizing the environmental impact of waste disposal.
Effective Utilization Of By Products During Incineration
The waste materials are gathered together and subjected to an incinerator process for the burning of organic substances. This cremation method releases waste into the environment, resulting in acid rain, contagious diseases, and wasted heat energy. This research highlights the effective utilisation of heat energy, flue gases, and ash content for the benefit of all living organisms, including humans and animals, as breathing in toxic air has negative side effects.
Ash
The garbage is loaded from the top, and after the incineration process, the ash is removed through the ash door. The ash is in the form of solid chunks that can be used efficiently for both commercial and residential building. It can also be used for road construction.
Flue gases
As a byproduct of the incineration process, a combination of several gases known as flue gas is produced. These gases are discharged into the environment and are the root cause of a variety of ailments, including asthma, lung cancer, and heart attacks, which indirectly leads to the premature death of living things. This research examines the effective utilisation of the gases produced during combustion. Incineration releases mostly nitrogen dioxide, carbon dioxide, sulphur dioxide, water vapour, and trace amounts of oxygen. As sulphur dioxide is a potent oxidizer, sulphur can be recovered from it via the Claus method. Hydrogen sulphide therefore reduces sulphur dioxide to produce elemental sulphur.
SO2 + 2 H2S – 3 S + 2 H2O
The elemental sulphur can undergo chemical reactions to produce dentally useful sulphur compounds such as sodium thiosulfate. Additionally, nitrogen dioxide, oxygen, and water are byproducts of the combustion process. Using Ostwald’s technique, around 98% of nitric acid can be produced when NO2, oxygen, and water react at 4 to 10 atmospheres at 217 degrees Celsius.
4 NO2 (g) + O2 (g) + 2 H2O (l) – 4 HNO3 (aq)
This nitric acid is utilised in crop cultivation. This will increase production and enable farmers to cultivate higher-quality crops.
Heat
Utilizing waste heat by turning it to power is possible. The Seebeck effect is utilised to convert heat to energy in thermoelectric generators. Thermoelectric materials utilise a phenomena that converts the difference in temperature into an electric potential. Bismuth telluride is a widely employed thermoelectric material. Currently, there are frequent power outages in every city in India; this power generation technology will employ waste materials to generate electricity, hence lowering the country’s electricity crisis.
Air Pollution Control
The combustion of municipal solid waste generates significant amounts of flue gases. The flue gases contain leftovers from incomplete combustion as well as a variety of hazardous contaminants. The content of the burned trash and the conditions of combustion determine the contaminants and their concentration. However, these gases contain ash, heavy metals, and other organic and inorganic substances.
There are particles (dust) and gases such as HCl, HF, and SO2 present. Certain toxic substances, such as mercury, dioxins, and NOx, can only be eliminated by the use of sophisticated and expensive chemical treatment procedures. Primary measures, which are initiatives that impede the creation of pollutants, primarily NOx and organic compounds such as dioxins, must be implemented to the greatest extent possible.
The air pollution control (APC) system is composed of electrostatic precipitators, bag house filters, dry, semi-dry, and wet acid gas removal systems, catalysts, and other similar components. Pollutants may be precipitated, adsorbed, absorbed, or transformed by secondary means.
The selection of an APC system is essentially determined by the actual emission restrictions or standards, if applicable, and the intended emission level. In this perspective, the various APC systems might be categorised as fundamental, intermediate, or advanced emission control.
Air Pollution Control Technology
Following are the equipment for the control of air pollution:
- Mechanical collectors (cyclones and multicyclones).
- Wet scrubbers (such as Venturi scrubbers).
- Fabric filters (bag house filters).
- Electrostatic precipitators (ESPs).
1. Mechanical collectors (cyclones and multi- cyclones)
Mechanical collectors (such as the cyclone) are ineffective in reducing the dust concentration of flue gas to 150 mg/Nm3 or less. As a result, they are only useful as a part of a more complex flue gas treatment system or as a secondary dust arrestor in hoppers and similar installations. Wet scrubbers (Venturi scrubbers and electric precipitators) can be built to meet a certain emission limit value, such as 100 mg/Nm3. Scrubbers are impractical as the sole or primary air pollution management technology, as the water applied will also remove the majority of the HCl from the flue gas. As a result, it will generate a dust-laden, caustic waste water stream with a pH of approximately 0. Fabric filters have a naturally high cleaning effectiveness, and whether or not they are required, they will remove particles down to around 10 mg/Nm3. However, cloth filters functioning directly on the boiler’s gases are susceptible to fluctuations in temperature, humidity, and spark carryover. In addition, they must be bypassed during the plant’s startup and shutdown.
Cyclone
- Application • Dust collector
- Emission level • 500 mg/Nm3
Working principle: The concept of operation is that the dust-laden gas is introduced tangentially and rotated. Dust particles collide with the wall and fall into the conical bottom, where they are collected, as a result of centrifugal forces. The flue gas is discharged through the middle outlet.
2. Venturi scrubber
- Application • Dust collector
- Emission level • About 100 mg/Nm3
Working principle: The dust-laden gas accelerates through a throat (a Venturi), atomizing the water that has been injected. Dust particles are collected by water droplets, which are then precipitated in a chamber resembling a cyclonic settling chamber.
3. Electrostatic precipitators
- Application • Dust collector
- Emission level • 20-150 mg/Nm3
Working principle: The dust-laden gas is directed into a box containing a number of suspended, grounded collection plates. Between each plate row are discharge electrodes negatively charged by rectified high-voltage DC. This produces an electric field, which charges the particles and causes them to migrate to the plates, generating a coating of dust. The plates are occasionally shook, causing the dust to fall into the bottom hopper.
4. Fabric filter
- Application • Dust collector
- Emission level • 10 mg/Nm3
Working principle: The dust-laden gas enters a box, where it is suctioned or compressed through cylindrical bags. A layer of dust accumulates on the surface (most often, the outer surface, in which case the bags are supported by cages). This layer is eliminated via a combination of shaking techniques.
Applications of Incinerator
Incinerators are used in a variety of applications, including:
- Municipal solid waste disposal: Incinerators are used to burn municipal solid waste (MSW) in order to reduce the volume of waste and prevent the release of pollutants into the environment.
- Hazardous waste disposal: Incinerators are used to burn hazardous waste, such as medical waste, chemical waste, and radioactive waste, in order to reduce the risk of contamination and protect the environment.
- Industrial waste disposal: Incinerators are used to burn industrial waste, such as waste from manufacturing processes, in order to reduce the volume of waste and prevent the release of pollutants into the environment.
- Sewage sludge disposal: Incinerators are used to burn sewage sludge in order to reduce the volume of waste and prevent the release of pollutants into the environment.
- Livestock waste disposal: Incinerators are used to burn waste from livestock operations, such as manure, in order to reduce the volume of waste and prevent the release of pollutants into the environment.
- Air pollution control: Incinerators are used to burn off waste gases, such as volatile organic compounds (VOCs), in order to prevent their release into the atmosphere.
- Energy recovery: Incinerators can also be used to recover energy from the waste that is burned. This can include electricity, steam, or hot water.
- Medical waste: Incineration is the most common method for treatment and disposal of medical waste.
- Marine waste: Incineration is an effective way of treating and disposing of waste from ships and boats.
- Food waste: Incineration is also a solution for food waste treatment and disposal.
- Pharmaceuticals : Incineration is also a solution for pharmaceuticals waste treatment and disposal.
Note that some of these applications may not be allowed in certain countries or regions, as they have different regulations and laws regarding incineration.
Advantages of Incinerator
- Volume reduction: Incineration can reduce the volume of waste by up to 90%, making it easier to store and transport the remaining ash.
- Pathogen destruction: Incineration can kill bacteria, viruses, and other pathogens that are present in the waste, making it safer to handle and dispose of.
- Pollutant destruction: Incineration can destroy pollutants that are present in the waste, such as volatile organic compounds (VOCs), heavy metals, and other toxic compounds.
- Energy recovery: Incinerators can recover energy from the waste that is burned, such as electricity, steam, or hot water, making it a more sustainable solution.
- Reduced land usage: Incineration reduces the amount of land needed for waste disposal and eliminates the need for landfills.
- Reduced greenhouse gas emissions: Incineration reduces the greenhouse gas emissions associated with other waste management methods, such as landfills, which release methane and other gases.
- Air pollution control: Incineration can be used to burn off waste gases, such as volatile organic compounds (VOCs), in order to prevent their release into the atmosphere.
- Medical waste: Incineration is the most common method for treatment and disposal of medical waste.
- Marine waste: Incineration is an effective way of treating and disposing of waste from ships and boats.
- Food waste: Incineration is also a solution for food waste treatment and disposal.
- Pharmaceuticals : Incineration is also a solution for pharmaceuticals waste treatment and disposal.
- Reduced Quantity of Waste: Depending on the components of solid waste, incinerators can reduce the amount of garbage by up to 95 percent and the amount of solid waste by up to 80 to 85 percent. Thus, combustion minimises reliance on landfills. Even though incinerators do not totally eliminate the need for a landfill, they greatly reduce the amount of area required. This is especially beneficial for countries with limited space, such as Japan, because landfills consume vast amounts of land that could be used for other economic purposes. Furthermore, the ash that results from the combustion of garbage is cheaper to carry than unburned waste, and it reduces liability concerns.
- Production of Heat and Power: Incineration plants convert garbage into energy that can be utilised to generate electricity or heat. During the 1950s, when energy costs were rising, many nations utilised the heat and energy produced by waste incinerators to generate electricity by means of steam turbines. The created energy can subsequently be used to power the requirements of surrounding residents. Cold-climate nations use the heat from the incinerators to warm their homes and workplaces in the vicinity of the plant. Europe and Japan have integrated incinerators into their modern heating systems, and Sweden meets 8% of its heating demands with garbage incinerators. On average, a single facility may burn up to 300 million tonnes of rubbish every year, transforming a portion of it into energy and lowering the strain on coal-fired power plants, which are an environmental disaster.
- Reduced Reliance on Transportation: Due to their low land requirements, waste incineration plants can be located near urban areas. This is helpful since it reduces the distance waste must be transported for disposal. This dramatically reduces the cost of transportation and the emissions of hazardous gases from automobiles during transit, hence reducing the overall carbon footprint. The money saved on transportation can then be used for other purposes, such as promoting the health of the community and fostering the expansion of a city or district.
- Better Control Over Odor and Noise: Instead of allowing waste to decompose in the open air, which contributes to air pollution, waste is burned inside a facility where the byproducts of the incineration process can be regulated, resulting in less offensive odour. Moreover, the creation of methane in landfills may result in explosions that create noise pollution, which is unheard of with incineration plants.
- Prevents the Production of Methane Gas: The decomposition of garbage in landfills generates huge quantities of methane, a major contributor to global warming. Methane is both harmful to the environment and flammable, making it a safety threat. They are safer and more environmentally friendly because they do not emit methane.
- Eliminates Harmful Germs and Chemicals: Incineration plants employ extremely high temperatures to eliminate hazardous microorganisms and chemicals in garbage. Thus, it is a highly successful strategy for decreasing clinical waste.
- Operates in Any Weather: Due to the enclosed structure of garbage incinerators, they may operate regardless of the weather. During the rainy season, for instance, waste cannot be put in a landfill since the rain will likely wash dangerous chemicals into the ground and form leachate, poisoning the subsurface water and surrounding land. Waste cannot be dumped while there is wind because it will be blown into the environment. In contrast, incinerators are not susceptible to weather fluctuations because they burn garbage without leaking. Incineration plants operate 24 hours a day and are more effective at trash management than landfills.
- It has a Computerized Monitoring System: Governments, towns, institutions, and commercial waste management firms can purchase an incinerator equipped with a computer device for the diagnosis of the majority of issues. This will allow operators to detect an issue before it worsens and becomes prohibitively expensive to rectify. A computer will also facilitate the work of operators, as they will be able to monitor the incinerator plant’s operational efficiency.
It is important to note that while incineration has many benefits, it also has some limitations and it is important to ensure that it is properly controlled and regulated to minimize negative impact on the environment and human health.
Disadvantages of Incinerator
Incinerators also have several disadvantages, including:
- High costs: Incineration can be expensive to build, operate and maintain.
- Air pollution: Incineration can release pollutants into the air, such as particulate matter, dioxins, and other pollutants.
- Ash disposal: Incineration produces ash, which can contain pollutants and heavy metals. This ash must be properly managed and disposed of.
- Odor: Incineration can produce odors that can be unpleasant for nearby residents.
- Noise: Incineration can produce noise that can be disruptive for nearby residents.
- High Operating Costs: The building of a waste incineration facility is a costly endeavour, mostly due to the infrastructure and equipment required to construct an incineration plant. In addition to its high initial cost, a trash incineration plant necessitates the hiring of skilled and devoted operators. The regular maintenance of the plant, which grows as the plant matures, adds another significant operating expense to a waste incinerator.
- Health risks: Incineration can pose health risks to workers and nearby residents, such as respiratory problems, cancer, and other health issues.
- Limited waste types: Incineration is not suitable for all types of waste, such as wet or bulky waste, and certain types of hazardous waste.
- Not a recycling solution: Incineration is not a recycling solution and it doesn’t allow to recover or separate the recyclable materials.
- Environmental Racism: It refers to any policy, practise, or instruction that disadvantages individuals, groups, or communities based on race or colour, whether intentionally or unintentionally. These so-called waste-to-energy plants are typically constructed in less affluent regions, particularly those with poor representation. This is a regular occurrence among minority groups and has severe negative effects on the local population.
- Does Not Contribute to Waste Reduction: Incineration is not conducive to recycling or trash reduction. This is not a strategy employed by any community. Priority should be placed on minimising trash and recycling the majority of it. Simply combusting the majority of waste without recycling part of it may create environmental harm since it may stimulate additional waste creation.
- Not a sustainable solution: Incineration uses fossil fuels and it has environmental impacts and carbon footprint.
- Dependence on fuel: Incineration requires a steady supply of fuel to operate, which may not always be available or sustainable.
- Not suitable for every location: Incineration may not be suitable for every location, depending on factors such as population density, air quality, and zoning regulations.
It is important to note that while incineration has some disadvantages, it can be an effective waste management solution when properly designed, operated, and regulated. It is important to weigh the benefits and drawbacks of incineration and consider other waste management options before implementing an incineration program.
Precautions
When operating an incinerator, it is important to take certain precautions in order to minimize negative impacts on the environment and human health. These precautions include:
- Adequate pollution control: Incinerators must be equipped with adequate pollution control equipment, such as filters, scrubbers, and other devices, to prevent the release of pollutants into the air.
- Proper ash disposal: Incineration produces ash, which can contain pollutants and heavy metals. This ash must be properly managed and disposed of in a way that minimizes the risk of contamination.
- Emission monitoring: Incinerators should be regularly monitored for emissions to ensure that they are operating within legal limits and to identify any potential problems.
- Proper maintenance: Incinerators must be properly maintained to ensure that they are operating efficiently and to minimize the risk of breakdowns or accidents.
- Emergency preparedness: Incinerators should have emergency preparedness plans in place to respond to any accidents or malfunctions that may occur.
- Training: Incinerator operators should be properly trained to operate the equipment safely and effectively.
- Compliance with regulations: Incinerators must comply with all local, state, and federal regulations and laws, including air quality regulations and waste management regulations.
- Community engagement: Incinerator operators should engage with the local community and be transparent about their operations, providing information about the facility’s performance and addressing any concerns that may arise.
- Not suitable for every type of waste: Incineration is not suitable for all types of waste, such as wet or bulky waste, and certain types of hazardous waste.
- Not recycling solution: Incineration is not a recycling solution and it doesn’t allow to recover or separate the recyclable materials.
- Not sustainable solution: Incineration uses fossil fuels and it has environmental impacts and carbon footprint.
By following these precautions, incinerator operators can minimize negative impacts and help ensure that incineration is used responsibly and sustainably.
What we Cannot burn in incinerator?
There are certain types of materials that should not be burned in an incinerator, as they can release harmful pollutants into the air or cause damage to the incinerator itself. Some examples of materials that should not be burned in an incinerator include:
- Hazardous waste, such as chemicals, batteries, and pesticides, as they can release toxic fumes when burned.
- Medical waste, such as sharps, pathological waste, and biohazardous waste, as they can pose a risk of infection to workers handling the waste and to people living near the incinerator.
- Asbestos, as it can release fibers into the air when burned, which can be harmful to human health.
- Plastic, as it can release harmful pollutants when burned and can damage the incinerator itself.
- Whole tires, as they can release harmful pollutants when burned, such as dioxins, furans, and heavy metals, and can also damage the incinerator.
- Electronic waste, as it can release lead, mercury, and other toxic pollutants when burned.
It’s important to note that regulations vary by location and the specific type of incinerator being used. Always check with local authorities for specific regulations regarding what can and cannot be burned in an incinerator.
Why are incinerators used?
Incinerators are used for a variety of reasons, including waste disposal, energy generation, and pollution control.
- Waste disposal: Incineration is used as a method of waste disposal because it reduces the volume of solid waste and eliminates the need for landfills. Incineration can be used to dispose of a wide variety of waste materials, including municipal solid waste, medical waste, hazardous waste, and sewage sludge.
- Energy generation: Incineration can also be used to generate electricity by using the heat generated during the burning process to power a steam turbine. This is known as waste-to-energy (WTE) technology. WTE plants can generate electricity from a variety of waste materials, including municipal solid waste and agricultural waste.
- Pollution control: Incineration can be used as a pollution control measure by destroying pollutants before they are released into the environment. This is often used for the treatment of hazardous waste, such as industrial chemicals and pesticides, to prevent their release into the air, water, or soil.
- Medical waste: Medical waste is defined as any waste materials that have been contaminated with blood, body fluids, or other potentially infectious materials. It’s considered one of the most effective ways to destroy medical waste, as it uses high temperatures to sterilize the waste and reduce its volume.
It’s important to note that regulations vary by location and the specific type of incinerator being used. Always check with local authorities for specific regulations regarding what can and cannot be burned in an incinerator.
Is incineration better than recycling?
It depends on the specific context and materials in question. Both incineration and recycling have their own advantages and disadvantages, and the best approach will depend on the specific waste materials, local regulations and resources, and the overall goals of waste management.
- Incineration: Incineration is an effective way to reduce the volume of waste and eliminate the need for landfills. It also can generate electricity in some cases. However, it can be expensive to build and operate an incinerator, and it can release pollutants into the air if not properly controlled. Additionally, incineration doesn’t recover valuable resources like recycling does.
- Recycling: Recycling is a cost-effective way to conserve natural resources and reduce pollution by reducing the need to extract new raw materials. It also creates jobs and economic activity in the recycling and manufacturing industries. But, not all materials are recyclable and some recyclable materials need to be cleaned, sorted and processed before being recycled, which can be expensive.
So, when it comes to waste management, it’s important to consider the overall goals, and choose the approach that will best achieve those goals in a cost-effective and environmentally friendly way. Both incineration and recycling can play a role in achieving these goals, but it’s important to evaluate the specific materials and local resources and regulations to determine which approach is best.
How is incineration harmful?
Incineration can be harmful if not properly controlled, as it can release pollutants into the air and affect human health and the environment. Some of the potential harms of incineration include:
- Air pollution: Incineration produces flue gases that contain pollutants such as particulate matter, dioxins, furans, and heavy metals, which can harm human health and the environment if not properly controlled.
- Greenhouse gas emissions: Incineration produces greenhouse gases such as carbon dioxide, which contribute to climate change.
- Resource depletion: Incineration destroys valuable resources that could be recycled or reused.
- Noise pollution: Incineration facilities can produce noise pollution that can disturb local communities.
- Health risks: The emissions from incineration can contain harmful pollutants that can have adverse effects on human health, such as respiratory problems, cancer, and other illnesses.
It’s important to note that regulations vary by location and the specific type of incinerator being used. Always check with local authorities for specific regulations regarding what can and cannot be burned in an incinerator. With proper control and management, modern incineration facilities are designed to minimize the release of pollutants into the air and meet the stringent emission standards set by the authorities to minimize the potential harm.
FAQ
What incinerator means?
An incinerator is a device used to burn waste materials, typically as a method of disposal. Incineration is a process of thermally oxidizing waste materials in the presence of oxygen to convert them into ash, flue gas, and heat. Incineration is used to dispose of a wide variety of waste materials, including municipal solid waste, medical waste, hazardous waste, and sewage sludge. It is also used to generate electricity in some cases.
What is incinerator in hospital?
An incinerator in a hospital is a device used to burn medical waste, which is defined as any waste materials that have been contaminated with blood, body fluids, or other potentially infectious materials. Medical waste can include sharps (such as needles, scalpels, and syringes), pathological waste (such as tissue samples), and biohazardous waste (such as lab cultures and animal carcasses).
Incineration is considered one of the most effective ways to destroy medical waste, as it uses high temperatures to sterilize the waste and reduce its volume. Incinerators used in hospitals typically have advanced filtration systems in place to capture any pollutants that may be released during the burning process. These systems may include scrubbers and filters that remove pollutants such as dioxins, furans, and particulate matter.
Hospital incinerators are regulated by local authorities and are required to meet specific emission standards. They are also typically subject to regular inspections to ensure they are operating safely and effectively.
What is the principle of incinerator?
An incinerator is a device that burns waste materials in the presence of oxygen to convert them into ash, flue gas, and heat. The basic principle of an incinerator is thermally oxidizing the waste materials to reduce the volume of the waste and eliminate the need for landfills. The process of incineration is typically divided into three main stages: drying, combustion, and post-combustion. The drying stage removes moisture from the waste, the combustion stage burns the waste at high temperatures, and the post-combustion stage treats the flue gases to remove pollutants before they are released into the atmosphere. Incinerators are equipped with advanced filtration systems to capture pollutants, including scrubbers and filters, to remove pollutants such as dioxins, furans, and particulate matter. This ensures that the incineration process is safe and environmentally friendly.
Do incinerators pollute air?
Incinerators can release pollutants into the air if not properly controlled. Incineration process produces flue gases that contain pollutants such as particulate matter, dioxins, furans, and heavy metals. These pollutants can be harmful to human health and the environment. Therefore, it is important that incinerators are equipped with advanced filtration systems, such as scrubbers and filters, to remove these pollutants before they are released into the atmosphere.
Additionally, the emissions from incinerators are regulated by local authorities and are required to meet specific emission standards, which vary by location. Regular inspections are also conducted to ensure that the incinerators are operating safely and effectively.
However, with proper control and management, modern incineration facilities are designed to minimize the release of pollutants into the air and meet the stringent emission standards set by the authorities.
Can plastic be incinerated?
Plastic can be incinerated, but it’s not considered a recommended method of disposal due to the potential negative environmental and health effects. Plastic releases pollutants such as hydrochloric acid, sulfur dioxide, and dioxins when burned, which can harm human health and the environment. Additionally, burning plastic can also damage the incinerator itself.
Plastic is not considered a suitable waste for incineration since it is not a good source of energy, it has low calorific value, and it produces toxic pollutants when burned. Instead, plastic waste should be recycled or processed in a facility specifically designed to handle plastic waste, such as a pyrolysis or gasification plant.
It’s important to note that regulations vary by location and the specific type of incinerator being used. Always check with local authorities for specific regulations regarding what can and cannot be burned in an incinerator.
References
- Zjup, Wdse & Bourtsalas, Athanasios & Huang, Qunxing & Zhang, Hanwei & Themelis, Nickolas. (2020). Energy recovery in China from solid wastes by the moving grate and circulating fluidized bed technologies https://rdcu.be/b3jg1. 2. 27-36.
- Lombardi, F., Lategano, E., Cordiner, S., & Torretta, V. (2013). Waste incineration in rotary kilns: a new simulation combustion tool to support design and technical change. Waste Management & Research, 31(7), 739–750. doi:10.1177/0734242×13484187
- https://microbenotes.com/incinerator-principle-procedure-parts-types-uses-examples/
- https://www.rpi.edu/dept/chem-eng/Biotech-Environ/incinerator.html
- https://slideplayer.com/slide/10814404/
- https://www.inciner8.com/blog/waste-management/what-are-incinerator-machines-an-idiots-guide
- https://www.inciner8.com/how-an-incinerator-works
- https://www.irjet.net/archives/V4/i12/IRJET-V4I1270.pdf
- https://www.conserve-energy-future.com/advantages-and-disadvantages-incineration.php
- https://www.marineengineersknowledge.com/2021/06/incinerator.html
- https://www.epa.gov/sites/default/files/2015-04/documents/a_citizens_guide_to_incineration.pdf
- https://frtr.gov/matrix2/health_safety/chapter_24.html
- Text Highlighting: Select any text in the post content to highlight it
- Text Annotation: Select text and add comments with annotations
- Comment Management: Edit or delete your own comments
- Highlight Management: Remove your own highlights
How to use: Simply select any text in the post content above, and you'll see annotation options. Login here or create an account to get started.