What is Natural Rubber?
- Rubber is primarily derived from the latex of various tropical and subtropical plants, particularly those from families such as Moraceae, Euphorbiaceae, and Apocynaceae. While over fifty species can produce rubber, only a few are of significant commercial value. Historically, wild trees were the primary source of rubber, but today, plantation-grown rubber supplies about 95% of the global demand. This shift marks a significant milestone in the rubber industry, which has evolved rapidly over the past century.
- Rubber, as a globally important crop, is relatively young, with commercial cultivation beginning just over 50 years ago. The dramatic increase in plantation rubber production—from 1,000 tons in 1907 to over 620,000 tons by 1928—demonstrates the remarkable progress of modern agriculture. However, this rapid development has not been without challenges. Overproduction has periodically caused financial instability within the industry, leading to attempts at regulating output, particularly by British-controlled plantations in regions like Malaya. Additionally, the advent of synthetic rubber, developed through years of research, has introduced competition to natural rubber, posing further challenges to the traditional rubber industry.
- Latex, the substance from which rubber is extracted, is produced in specialized cells within the bark, leaves, and soft tissues of rubber plants. Commercially viable latex is mainly harvested from the lower part of the tree trunk and, in some species, from aerial roots. Latex is a sticky, white liquid containing a mixture of water, hydrocarbons, resins, proteins, and caoutchouc—the component responsible for rubber production. The biological purpose of latex in plants is not entirely understood, though it may assist in healing wounds.
- The unique properties of rubber have been known for centuries. Indigenous peoples of Central America were familiar with its uses and referred to it as “cahuchu,” a term that evolved into the modern “caoutchouc.” Although Christopher Columbus introduced rubber to Europe, it did not gain widespread recognition until 1735. In 1770, the substance was named “rubber” by Joseph Priestley, after observing its ability to erase pencil marks. Technological advances, such as Charles Mackintosh’s waterproofing process in 1823 and Charles Goodyear’s vulcanization discovery in 1839, significantly boosted rubber’s industrial applications, leading to the creation of countless products that utilize rubber today.
- Despite these advancements, natural rubber remains crucial to industries worldwide. However, its future may be influenced by ongoing developments in synthetic alternatives.
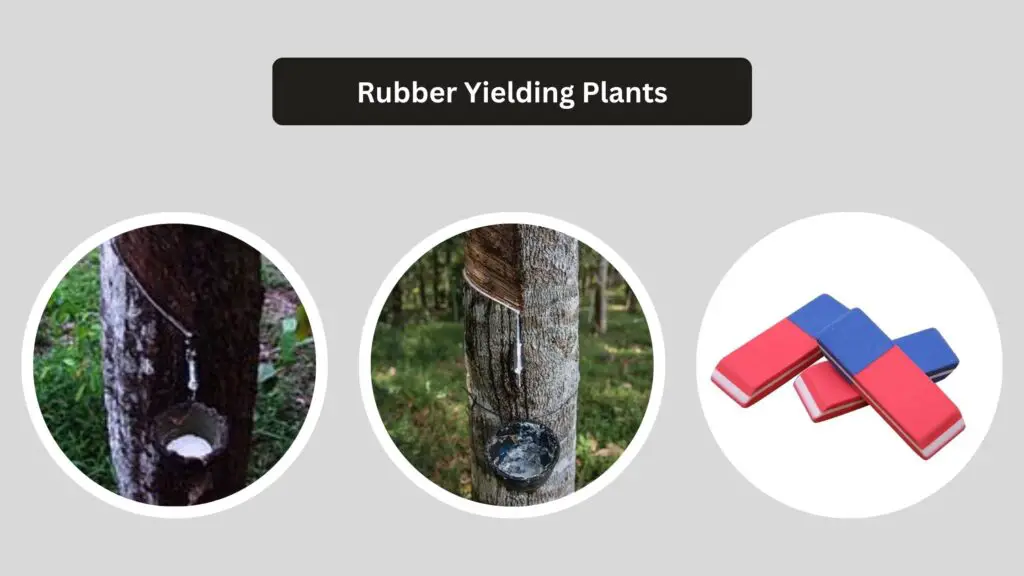
Para Rubber
The Para rubber tree (Hevea brasiliensis) is the main source of natural rubber, contributing 90-95% of the world’s rubber production. This species is indigenous to the Amazon and Orinoco river valleys in South America, where the hot, humid climate provides optimal growing conditions. The region, spanning over one million square miles, contains an estimated 300 million Para rubber trees. These trees thrive in areas with a consistent temperature range of 75°F to 90°F and an annual rainfall of 80 to 120 inches.
- Tree Characteristics:
- Para rubber trees can live for up to 200 years, growing to heights of 60 to 100 feet and girths of 8 to 10 feet.
- The leaves are three-lobed, and the flowers are small and not visually striking.
- The fruits house three seeds, each containing 23% to 32% fatty oil, sometimes extracted for use as a drying oil. The leftover oil cake, rich in protein, serves as animal feed.
- Though these trees are most commonly found in floodplain islands, they also occur on uplands.
- Wild Rubber Collection:
- The extraction of latex from wild trees is managed by workers known as “seringuieros.” These laborers, employed by rubber estate owners, locate suitable trees and make incisions in the bark using an axe or similar tool.
- Small cups are placed beneath these cuts to collect the latex, which flows for several hours before being transferred to larger vessels.
- The latex is brought to camps where it undergoes coagulation. Fires made from palm nuts produce dense smoke containing acetic acid, creosote, and tars.
- Workers dip paddles into the latex and expose them to the smoke, causing the latex to coagulate and form a layer of crude rubber. This process is repeated until a ball of rubber, weighing between 20 and 100 pounds, is produced.
- The resulting rubber is impure, often containing about 15% water. Although other Hevea species also yield rubber, they are not as widely used as Hevea brasiliensis.
- Plantation Rubber Production:
- Para rubber has been successfully introduced to various tropical regions with similar rainforest environments. By 1929, over 6 million acres of land, mainly in places like Ceylon, Malaya, Java, and Sumatra, were devoted to rubber plantations.
- Every stage of production—planting, cultivation, tapping, and coagulation—has been meticulously studied to optimize the yield.
- Rubber trees thrive at altitudes up to 2,000 feet, and they are propagated from seeds grown in nurseries before being transplanted to plantations. In some cases, grafting or budding is used to propagate trees.
- The trees grow quickly, and tapping can begin at around five years of age, although older trees tend to yield more latex.
- Tapping Methods:
- Several tapping techniques are employed to harvest latex. In the “herringbone” method, oblique cuts are made leading to a central vertical cut. Spiral and one-sided cuts are also used.
- The goal is to sever as many latex vessels as possible while cutting close to the cambium layer, which promotes wound response and increases latex production.
- Tapping typically occurs in the mornings and sometimes continues during wet weather. Instruments such as mallets and chisels are used to make thin incisions.
- Once these cuts reach a width of 1.5 inches, they are allowed to heal. The latex flows for about 30 minutes after reopening the cuts and is collected in aluminum cups. The yield from each tree can reach up to 25 pounds.
- Coagulation and Processing:
- After collection, latex is strained to remove impurities. Water or formalin may be added. There are several methods for coagulation:
- Latex is poured onto enameled iron plates, acetic acid is added, and the mixture is left to sit for 12 hours to coagulate.
- The coagulated cake is rolled flat and left to dry for several weeks. The rubber is then packed for shipment.
- Sheet rubber is created by rolling coagulated latex into thin sheets, while “worm rubber” consists of irregular pieces cut from these sheets.
- Crepe rubber is produced by bleaching and washing coagulated latex in tanks, followed by passing it through a creping machine that produces thin, perforated strips of rubber. These strips are air-dried before being shipped.
- Sometimes, alternative coagulating agents like ammonia, formic acid (from ants), cigar smoke, and wood smoke are used.
- After collection, latex is strained to remove impurities. Water or formalin may be added. There are several methods for coagulation:
- Sprayed Rubber:
- A modern method of producing rubber involves converting latex into sprayed rubber. Latex is dropped onto whirling disks, and small particles of rubber are thrown off as moisture evaporates. This process produces rubber that is exceedingly pure and clean.
- Liquid latex is also imported in significant quantities into the United States. Ammonia is added to the latex to preserve it and prevent premature coagulation.
Different Sources of Rubber
Rubber is obtained from various plant sources across different regions of the world. Each source has its distinct characteristics, growth requirements, and methods of latex collection. While some sources have become commercially significant, others have struggled to compete with more efficient producers like Para rubber. The following outlines several important sources of rubber.
- Panama Rubber:
- Panama rubber is derived from Castilla elastica, a tall tree native to Mexico and Central America, and has been in use since 1875.
- The tree thrives in deep loamy soil on high ground and requires temperatures above 60°F with shade during its early growth stages. It can reach up to 150 feet in height.
- Initially, trees were cut down to maximize latex yield, leading to near extinction. Today, more conservative tapping methods are employed. The trees are tapped at 8 to 10 years of age, producing up to 50 pounds of latex.
- Latex coagulation is achieved using plant juices, alum, boiling, or air exposure. The crude rubber is shipped in flat cakes. Despite its cultivation in Central America, Panama rubber cannot compete commercially with Para rubber in other regions.
- Ceara Rubber:
- Manihot glaziovii, the source of Ceara rubber, is native to the arid regions of Brazil. It grows rapidly, even in dry, rocky soil unsuitable for other rubber plants, and reaches a maximum height of 30 feet within a few years.
- The trees are tapped at 4 to 5 years of age and produce a good grade of rubber. Coagulation of the latex occurs through air or smoke exposure, and the crude rubber is exported in blocks or flat cakes.
- Ceara rubber is now cultivated in regions like Ceylon, India, and other tropical countries.
- Assam Rubber:
- Known as India rubber, Ficus elastica is native to northern India and Malaya, thriving in hot climates with substantial rainfall.
- The tree often begins its life as an epiphyte and grows to considerable height, developing large buttresses and prop roots. Both the roots and the stem are tapped for latex, which is allowed to drip onto bamboo mats for coagulation.
- The rubber is scraped off the trunk, cleaned, and dried. Historically, wild trees were tapped wastefully, but cultivation practices have been implemented. However, the yield is low, and trees do not mature until around 50 years of age, making Assam rubber commercially insignificant today.
- Lagos Silk Rubber:
- This rubber is obtained from Funtumia elastica, a large tree native to tropical West Africa. Discovered in 1894, its exploitation was so intense that the species was nearly driven to extinction by 1898, when over 6 million pounds were exported.
- Although efforts have been made to cultivate the tree and revive the industry, Para rubber plantations have since become the dominant source of rubber in West Africa.
- Landolphia Rubber:
- Several woody climbers from the genus Landolphia, such as L. Kirkii, L. Heudelotii, and L. owariensis, were once significant sources of African rubber.
- These large vines, often 6 inches in diameter, were cut down and chopped into pieces to extract latex, which was coagulated using plant juices or sun exposure. Wasteful harvesting methods were common, focusing on immediate yields without regard for sustainability.
- The most notable issue surrounding Landolphia rubber was the mistreatment of native workers during extraction, particularly in the Belgian Congo under King Leopold II. While wild Landolphia rubber still exists, its future is bleak due to poor harvesting techniques and impracticality for cultivation.
- Guayule Rubber:
- Parthenium argentatum, the only non-tropical plant used for rubber production, is native to the arid regions of Mexico and the southern United States.
- Unlike other rubber sources, guayule does not contain latex. Instead, small granules of caoutchouc are dispersed throughout its tissues, which are extracted mechanically or with solvents.
- The rubber quality is generally low, and yields are limited, but it has specific uses. One challenge in guayule production is the need to destroy the entire crop to obtain caoutchouc, unlike latex-yielding species. Despite this, cultivation is increasing due to its suitability for certain purposes.
- Minor Sources of Rubber:
- Several other plant species have been explored as potential rubber sources:
- Euphorbia intisy, a leafless shrub from the arid regions of Madagascar, produces latex that coagulates in elastic strands of high-grade rubber. Efforts are being made to cultivate it in the United States due to its adaptability to desert climates.
- Several native American plants, including the desert milkweed (Asclepias subulata), Indian hemp (Apocynum cannabinum), and goldenrods like Solidago leavenworthii, have also been experimented with for rubber production. In goldenrods, caoutchouc occurs as granules, and ongoing research offers hope for their future commercial use.
- Several other plant species have been explored as potential rubber sources:
Production and Use of Rubber
Rubber is one of the most indispensable natural products, playing a vital role in many industries. Its global production and diverse applications have evolved over time, with multiple regions contributing significantly to its trade. Here is a detailed breakdown of rubber production and its various uses, highlighting the processes and sources involved.
- Global Rubber Trade (1933):
In 1933, the global trade in crude rubber reached approximately 2.3 billion pounds. British Malaya was the leading exporter with 1.3 billion pounds, followed by the Dutch East Indies, which exported 750 million pounds, and Ceylon, with 142 million pounds. Other contributors included Indo-China, Borneo, Brazil, and India. - Rubber Consumption:
The United States is the largest consumer of rubber, utilizing nearly two-thirds of the global production. Other significant consumers include Great Britain, France, and Germany, with Great Britain using only a quarter of the amount consumed by the U.S. - Primary Uses of Rubber:
Over 85% of crude rubber is utilized in the production of tires and inner tubes, essential to the automotive industry. Rubber is also used in the manufacturing of boots and shoes, mechanical goods (such as hoses, tubes, and belts), waterproof clothing, and various druggist supplies. Other applications include insulated wire, electrical goods, toys, machine packing, and adhesives. - Hard Rubber:
Hard rubber is created through vulcanization, a process in which crude rubber is treated with 30% sulfur. This form of rubber has distinct properties, making it suitable for surgical appliances, as well as telephone and radio components.
Gutta-Percha
- Origin and Source:
Gutta-percha is a non-elastic type of rubber extracted from the latex of trees in the Sapotaceae family, particularly Palaquium Gutta. These trees are found in regions such as Borneo, Sumatra, and the Philippines. - Harvesting Process:
The latex is harvested by making incisions in the tree bark or by felling the trees. The latex, which flows slowly from the cuts, coagulates into grayish-yellow masses, which are later purified through boiling and washing. - Applications of Gutta-Percha:
This material is crucial in the manufacturing of submarine cables due to its resistance to saltwater and excellent insulation properties. Other uses include waterproofing, golf balls, telephone receivers, and adhesives.
Balata
- Origin and Characteristics:
Balata is derived from Manilkara bidentata, native to South America and Trinidad. This tree is tapped three times annually to collect latex, which coagulates in the air. - Uses of Balata:
Balata serves similar industrial purposes as gutta-percha. It is especially valuable for making machine beltings, thanks to its grip and elasticity. Additionally, balata is used as a substitute for chicle.
Jelutong
- Production and Use:
Jelutong is extracted from Dyera costulata, primarily in Malaysia. While it was briefly exploited as a rubber source between 1910 and 1915, its latex contains too many impurities, leading to its use as a chicle substitute rather than a rubber source.
Chicle
- Origin and Extraction:
Chicle is derived from Achras Zapota, commonly known as the sapodilla tree. Native to Mexico and Central America, its latex contains 20-25% gum. The gum is harvested using zigzag cuts on the tree trunk, with the latex flowing into collection bags. - Uses of Chicle:
Chicle is primarily used in the chewing gum industry. Raw chicle undergoes a purification process involving boiling, washing, and powdering before being mixed with flavoring agents. The United States consumes the majority of the global chicle supply.
Other Latex-Producing Trees
- Milk-Producing Trees:
Several trees from South and Central America, such as Brosimum utile and Couma guatemalensis, produce latex that is palatable and used locally as a substitute for milk. These “cow trees” have historical and potential industrial significance, particularly for their medicinal and nutritional properties.
Uses of Rubber
Rubber, due to its versatile properties, is employed across numerous industries. Here is a detailed breakdown of its various uses:
- Tires and Inner Tubes:
Over 85% of rubber production is dedicated to the automotive industry, specifically for the manufacturing of tires and inner tubes, essential components for vehicles. - Footwear:
Rubber is commonly used to produce boots and shoes, particularly those designed for waterproofing or durability. - Mechanical Goods:
Rubber is a key material in the production of hoses, tubes, belts, and other mechanical goods due to its flexibility and strength. - Waterproof Clothing:
Rubber’s impermeability to water makes it ideal for waterproof garments, such as raincoats, diving suits, and other outdoor gear. - Electrical Goods:
Rubber, being a poor conductor of electricity, is extensively used for insulating wires and other electrical components. This includes protective casings for electrical appliances and cables. - Medical and Laboratory Equipment:
Rubber is used to create various medical supplies, including gloves, tubing, and other sterile equipment, thanks to its flexibility and durability. In some cases, hard rubber is used for surgical instruments and appliances. - Adhesives and Cements:
Rubber serves as a binding agent in numerous industrial adhesives and cements due to its tacky and cohesive properties. - Toys and Recreational Items:
Rubber is used in the production of toys, including balls and other play equipment, due to its elasticity and resilience. - Seals and Packing Materials:
Rubber’s ability to form airtight and watertight seals makes it a preferred material for gaskets, O-rings, and other sealing applications in machinery and household items. - Gutta-Percha and Balata Uses:
Non-elastic rubbers like gutta-percha and balata are essential in more specialized applications, such as insulating submarine cables and making machine beltings. They are also used in golf balls, telephone receivers, and dental splints. - Chewing Gum:
Chicle, a natural latex related to rubber, forms the base for chewing gum. It is mixed with sugar and flavoring agents to create the final product.
- Perumal, Venkatachalam & Geetha, Natesan & Palanivel, Sangeetha & Thulaseedharan, Arjunan. (2013). Natural rubber producing plants: An overview. African Journal of Biotechnology. Vol. 12. 1297-1310. 10.5897/AJBX12.016.
- https://mdoner.gov.in/contentimages/files/9_1.pdf
- https://www.jsscacs.edu.in/sites/default/files/Department%20Files/rubber-notes%20pdf.pdf
- Text Highlighting: Select any text in the post content to highlight it
- Text Annotation: Select text and add comments with annotations
- Comment Management: Edit or delete your own comments
- Highlight Management: Remove your own highlights
How to use: Simply select any text in the post content above, and you'll see annotation options. Login here or create an account to get started.